Welcome to the Decarb Guidebook
Approach
Benchmarking
Building Codes & Design Standards
State & Local Regulations
Technologies: Load Reduction
Technologies: Dehumidification
Technologies: If you must have a gas-fired boiler
Technologies: Central Plant
Technologies: Domestic Hot Water
Technologies: Steam
Technologies: Load Shifting and Energy Storage
Technologies: Emerging Technologies
Motivation Program
Pilot Projects
How to Pay for Decarbonization
Community Discussions
Workshops
Executive Summary
Retro-commissioning of building controls enables an existing Building Automation System (BAS) to be used to its full capabilities. Many hospitals, even new facilities, will experience a degradation of building control and efficiency over time. Infrequent controls commissioning, lack of controls and energy monitoring, infrequent system and equipment maintenance, poor controls design from the start and/or poorly educated facility staff can all cause the degradation of building controls. If not addressed, it can cause operational issues, reduced occupant comfort, and increased energy consumption, along with shortening the useful life of HVAC equipment. Retro-commissioning and active commissioning at a regular interval can help prevent these problems from happening.
Many hospitals and buildings continuously go through changes in space usage which cause operational problems. A plan for recommissioning is established as part of the existing retro commissioning process.
Often, the building control systems are installed and made functional, but additional full-building system analysis is rarely done for the purpose of increasing efficiency. Designing a control system in this way will allow the facility to take advantage of the many energy saving features such as scheduling and setpoint reset, and ongoing commissioning ensures that the building maintains efficient performance.
Buildings that perform retro-commissioning can cut their electricity and natural gas use by up to 30% each! This is also typically a low-cost, low-payback project with the added benefit of extending the useful life of equipment and avoiding more costly issues from happening in the future.
Retro-commissioning (RCx)
Technical Description
What is retro-commissioning?
Retro-commissioning of building controls enables an existing Building Automation System (BAS) to be used to its full capabilities, often bringing improved system efficiencies beyond the originally designed system. According to Lawrence Berkeley Labs, retro-commissioning is a process that seeks to improve how building equipment and systems function together. Depending on the age of the building, retro-commissioning can often resolve problems that occurred during design or construction, or address problems that have developed throughout the building's life. In all, retro-commissioning improves a building's operations and maintenance (O&M) procedures to enhance overall building performance.
Degradation of building controls
Infrequent controls commissioning or continuous commissioning, a lack of controls and energy monitoring, infrequent system and equipment maintenance, poor controls design, understaffed facility departments, and/or poorly educated facility staff can all cause the degradation of building controls. If not maintained, the efficiency of building controls will degrade over time as issues build up. It is estimated that as control systems degrade, energy consumption increases by about 5-10% per year. Any savings realized from previous retro-commissioning projects can disappear in just 4-5 years.
One of the most common culprits is ‘operator override’. Often, a facility will experience a ‘hot call’ or ‘cold call’, which is when the room occupant complains of the space being too hot or cold, and override the current sequence of operations indefinitely. This override forces the control system to operate in a way that is different from its programming to temporarily fix a problem, such as an uncomfortable occupant. Once that problem has been resolved, the override could be forgotten and it would remain in place, causing future operational issues.
Implementing efficient controls strategies
The following are 8 common efficient control strategies that can be implemented during retro-commissioning to improve system performance and reduce energy consumption. These measures should be implemented and checked annually.
Minimum zone ventilation setpoint analysis
Many hospital spaces operate 24/7 with large airflows and specific temperature and humidity requirements, but are occupied less than 12 hours/day. Space pressure relationships and other regulatory requirements can be maintained with much lower airflow rates and relaxed temperature ranges. Reheat loads can be significantly reduced during these unoccupied periods.
Modify the minimum ventilation setpoint on VAV boxes based on current codes. The national standard for ventilation of healthcare facilities, ASHRAE 170, and the California ventilation standard, Title 24, Part 4, California Mechanical Code, Chapter 4 have changed in recent years to lower minimum rates in various zones. A regular study of zones and their operating minimum rates should be conducted every few years to ensure the building is following the most recent code-allowed minimum ventilation and taking advantage of the most efficient design allowed.
It was often the practice of engineers to set the minimum setpoint of VAV boxes to 50% of the maximum rather than basing it on the lowest air change rate allowed by code. In addition, many code requirements have lowered over the last several years, such as Patient rooms which lowered from 6 ACH to 4 ACH. Calculating and setting the VAV minimums to the lowest allowable minimum setpoint can save fan, reheat, and cooling energy throughout the year. The table below shows how historical air change rates have changed over the years. [1]
Table 1: Historical Air Change Rates for Healthcare Facilities from ASHRAE 170.
Supply air temperature reset (SATR)
Standard control strategy for air handling units has been a constant-temperature discharge. Resetting supply air temperature based on actual cooling demand reduces the need for reheat as a means of space temperature control. This measure will poll boxes to determine if the majority of the terminal boxes are reheating, which would mean the supply air temperature is too cold for the current demand.
Implement automatic reset of air handling unit (AHU) supply air temperature setpoint to respond to actual zone demand. A control sequence can poll zones to determine if supply air temperature is colder than necessary, which results in increased cooling and zone reheating. The system also ensures that comfort is maintained by lowering the supply air temperature when needed.
SATR is used to automatically refine the operation of HVAC systems, reducing fan, heating, and cooling costs significantly. Typically, implementing SATR will allow the supply air temperature to rise from a typical setpoint of 55F to 60-65F based on outside temperature, while concurrently keeping the room temperature and relative humidity at set points that are needed.
Figure 1: Supply Air Temperature Reset Sequence of Operations, ASHRAE Standard 36: High Performance Sequences of Operation for HVAC Systems
Efficient SATR strategy utilizes a trim-and-response sequence in control system programming to take a poll of all reheat valve positions to determine if the supply air temperature can increase while still satisfying the zone with the least amount of reheat, or the reheat valve that is open the least. Regardless of OAT, the control system will use all of the system information to select the best discharge temperature that can satisfy the zones and use the least amount of energy.
One consideration when designing an SATR control sequence is that there can be “rogue” zones. Rogue zones are abnormally operating zones, typically operating with a space temperature setpoint too low for the system to satisfy. These zones are always at full cooling and are never satisfied. It only takes 1 rogue zone to essentially disable SATR and eliminate the potential energy savings. Certain zones should be left out of the polling sequence when determining when and how much to reset.
Fan static pressure reset
A standard practice for years was for the Testing and Balancing (TAB) agent to open up all VAV boxes and set the Static pressure setpoint so that the furthest box can reach its maximum CFM. This is a situation that seldom if ever occurs and causes the fan to work much harder than it needs to.
Implement automatic reset of the supply fan static pressure setpoint, based on VAV box damper positions. With fan static pressure reset, the control system looks at the damper position of every box that the AHU serves and resets the static pressure so that no box is greater than 95% open, reducing the fan energy considerably.
Similar to the supply air temperature reset, it is important to eliminate any rogue zones, such as constant volume boxes or boxes that may serve rooms that are always starved for air. These rooms should be addressed by either increasing the maximum setpoint on the VAV boxes or adding supplemental cooling.
With both Supply Air Temperature Reset and Fan Static Pressure Reset, it is important to limit how much control the occupants have of their thermostats. All it takes is one person raising their thermostat to 80 F or lowering it to 60 F, causing the damper or reheat to go full open and causing the AHU to raise or lower its temperature or increase its static pressure. These out-of-bounds zone setpoints create rogue zones, affecting both the air handling unit and upstream equipment such as chillers, boilers and pumps.
Airside economizer optimization
It should be regular practice to verify that AHU economizers are working properly and set them up to control based on enthalpy rather than temperature. Using dry-bulb temperature to control economizer operation will make the wrong decision at times, increasing the load due to too much outside air or ignoring an opportunity for economizer operation.
AHU economizers should be checked periodically for proper damper operation. It is not unusual for dampers to stick either open or closed, causing increased need for cooling and/or heating. It is important for the dampers to work properly to provide free cooling when available and for the outside air dampers to properly close to their minimum position when the outside air is either too cold or warm. Improper damper operation or control strategies can increase loads for cooling, heating or dehumidification.
Unoccupied setback and shutdown scheduling
Many hospital areas are not occupied nights and weekends, including administrative areas and some patient care areas. It is common for HVAC systems serving these areas to remain in operation during these unoccupied times. Since ventilation airflow is a significant factor in the amount of reheat needed for a facility, there is opportunity to save on heating energy, most commonly natural gas, as well as cooling and fan energy, by turning down or turning off the ventilation systems that serve those areas, when circumstances allow.
Where possible, scheduling of AHUs and VAV boxes can be added with unoccupied turndown. During times when the spaces are unoccupied and when allowed by code [2], ventilation should be reduced. Ventilation reset may be accomplished using different methods that suit specific areas, including the following:
- Occupancy sensors: private offices, as well as patient rooms and operating suites if allowed by the authority having jurisdiction (AHJ). In some cases, HVAC systems can be shut off when the lights are shut off.
- Occupancy schedules: A fancy way of saying "clocks". Non health-related spaces with known occupancy patterns can be shut off when unoccupied or outside normal hours of operation. Zone temperature sensors are often equipped with a button that can be programmed to override the occupancy schedule, so that users can restore occupied operation when working outside of normal hours.
- CO2 sensors: Otherwise known as demand controlled ventilation. The CO2 sensor is a way to measure the number of people in large gathering spaces such as open office areas, conference rooms, auditoriums or theaters and reduce ventilation to that space when those large spaces are empty or lightly occupied.
OR setback: A big scheduling opportunity is to reduce the air changes in the operating rooms when they are unoccupied, known as OR setback. According to the ASHE OR Setback Strategy guide, operating rooms may be unoccupied 40% or more of the time. Given operating rooms high air flow rates, which is a minimum requirement of 20 total air changes per hour (ACH) but often set to 25 ACH or more, and strict temperature and relative humidity (20-60%, ASHRAE 170) requirements, it is one of the most costly spaces to condition in a hospital and a great opportunity for significant energy savings. ASHRAE 170 allows OR ventilation to setback as low as 6 ACH when unoccupied, while also maintaining positive pressure and required humidity range. OR setback is typically done using a combination of time schedule, occupancy sensors, and/or a manual switchover for staff to override the setback in the event of an unplanned surgery. This strategy will only affect the high air flow rates needed, not the temperature or humidity settings of the space, however it is worth noting that temperature requirements of the OR may limit the type of setback strategy selected. By only affecting the air flow and not the temperature and humidity, the spaces can be brought up to compliance in a matter of minutes. Many hospitals still have 100% outside air systems serving operating rooms/delivery rooms in which only a minimum of 12 ACH is required. Exceptions need to be mentioned.
Chilled water supply temperature reset
While many areas of the hospital require low chilled water temperatures to maintain design criteria (particularly operating rooms), as a rule of thumb, each 1°F increase in chilled water temperature reduces the energy consumption of the chiller by 1 - 1.5% [3]. While this is often done by resetting the chilled water temperature based on outdoor air, a better option is to use the control system to monitor the position of the chilled water valves throughout the system and reset the temperature to a higher value if all of the valves are less than 90-95% open. One challenge of this strategy is that often the increased pump energy can easily offset the energy saved at the chiller. For this reason, this strategy should also include a pump differential pressure (Dp) reset with the pump pressure reset taking precedence. The system should lower the pump Dp to its lowest allowable setting first before raising the CHW temperature.
For critical spaces where humidity ratio is a factor, resting chilled water temperature may result in adverse effects by increasing the % H in spaces.
Heating hot water supply temperature reset
Hot water supply temperature reset is accomplished in a similar way to chilled water temperature reset, in that it utilizes the control system to monitor the position of the hot water valves at the AHUs and resets the temperature to keep the valve open the most below 95% open. This is a more effective control strategy than the old common way of doing temperature resets, which controls the temperature setpoint based on the outside air temperature, because it uses the data gathered by the control system to make decisions based on actual space demand. Hot water needs in hospitals are not necessarily a function of outdoor temperature.
Chilled Water and Hot Water pump differential pressure reset
Variable speed pumps are often set up to control a fixed differential pressure, based on worst-case full-load conditions. Pump energy is often wasted when maintaining a differential pressure that is usually higher than necessary to provide adequate flow in the system. Similar to the temperature resets, this strategy utilizes the valve positions to determine the Dp setpoint. As mentioned previously, the Dp setpoint reset needs to take priority over temperature reset as the pump energy saved usually outweighs the chiller or boiler energy saved.
Best practices
Existing building retrofits
When designing retrofits, it is important to understand how the major equipment is being controlled, whether any of these strategies are already in place, how the retrofit project could impact those strategies, and whether there are opportunities to incorporate any of these strategies into the retrofit project.
There are often limits to how much savings can be achieved due to the conditions and capabilities of the existing equipment and controls. If a facility has pneumatic controls, a top priority should be to replace those with direct digital controls (DDC) and upgrade the controls system software before implementing any new controls strategies.
New construction projects
While retro-commissioning is all about modifying existing systems to make them more energy efficient, it should be noted that all of these strategies should also be incorporated into renovation and new construction projects. All of the above strategies can be easily incorporated into new design projects, because it's a blank slate and all devices and equipment use modern digital controls.
In order to be able to take advantage of the large savings of reset strategies, the designer must select air terminal units for internal zones large enough to meet their peak cooling loads with air warmer than the design supply air temperature.
It is also necessary to sense the outdoor dewpoint temperature to avoid losing humidity control. Humidity and dewpoint sensors have historically been inaccurate instruments with substantial drift, so it is important to choose a quality instrument and maintain its calibration frequently.
How does this decarbonize?
Retro-commissioning strategies reduce both electric and natural gas energy consumption of a facility by improving the performance of the boilers, fans, pumps, chillers, and other systems. Many of the RCx measures have a big impact on reducing reheat, which is a large portion of the overall natural gas consumption of a building.
Accounting for an average of over 40% of total building energy, and over 75% of total natural gas use in an average hospital, zone reheat is the largest share of energy consumption and a major source of scope 1 emissions. Excessive or over-ventilation results in more reheat and an increased consumption of natural gas, as well as electricity due to increased cooling and fan energy. By resetting the supply air temperature, or turning down ventilation to unoccupied zones, considerable heating, cooling and fan energy is saved and can result in up to a 30% reduction of Scope 1 Natural Gas emissions and Scope 2 Purchased Energy emissions.
Back in 2012, the ASHRAE Advanced Energy Design Guide for Large Hospitals [4] identified supply air temperature reset as one of the larger energy reduction requirements in the Standard 90.1-2010 energy models performed by Pacific Northwest National Laboratory for the ASHRAE Standard 90.1 committee. “SATR was especially beneficial in the hospital model and is therefore included in this Guide as a strategy. Raising the supply air temperature by 5°F, when appropriate, can reduce reheat by approximately 50% because zones typically don’t reheat more than about 10°F on average.”
Implementation
Barriers: Codes
There are no code barriers to implementing retro-commissioning. However, codes do not actively promote or require the implementation of retro-commissioning.
Barriers: Culture
The biggest barrier to implementation can be the staff - both clinical and facilities. Clinicians may be concerned that they will be unaware if rooms are not ready to use - it is hard to tell what the air change rate is, unless control systems have clear indicators. Facilities staff may be reluctant to change the way systems operate because they are understaffed and don’t need the trouble of making changes. Facilities staff often have no incentive to reduce energy cost or emissions, but they have a large incentive to keep everyone comfortable.
One of the biggest roadblocks to retro-commissioning is getting staff buy-in on the changes and what they accomplish. Most hospital maintenance teams are understaffed and their top priority is patient safety and comfort. The proposed modifications are intended to do that and save money, but there can be some resistance because it is operating the systems differently than they are used to.
Strategy
To overcome the barriers, the best solution is communication. Communicate with facility staff and leadership on the issues and opportunities for retro-commissioning and energy efficiency. Training facility maintenance staff on what changes are being made is critical to the longevity of those changes. A strong communication plan can make a big difference for what gets done.
For OR setbacks, there are numerous ways to address staff and clinician concerns. In addition to occupancy sensors, a few operating rooms can be fully conditioned 24/7, so they are always ready to use in the event of an emergency surgery. Visual indication of room status, such as red light/green light indicators can relieve concerns as well. Lastly, educating the staff and clinicians on the importance of airflow setback and why it is being done, as well as how to read indicator lights and operate the setback override switch to properly prepare an operating room for an emergency surgery.
Regarding upfront costs, many utility companies are offering incentives to help pay for a good portion of the RCx work. For example, PG&E’s RCx Incentive program, called the Commercial Custom Incentives Program, includes both retrofit and retrocommissioning measures. Incentives are paid directly to the customer based on achieved annual energy savings at the rate of $0.06/kWh, $0.50/therm and $75/on-peak kW (subject to measure capping). Customers may participate in the program with previously identified measures or request an investigative audit funded by PG&E. After the measures are installed, PG&E’s engineering team will verify that the measures were installed per industry best practices. Customers can also take advantage of PG&E’s zero percent interest financing program to help implement measures.
Energy data analytics including fault detection as well as dashboards showing facility energy use for both internal staff and the general public to view will help drive motivation and education on why continuous commissioning is important and critical to healthcare building decarbonization.
Financial analysis and business case
The following estimates are derived from the US Department of Energy:
- A number of studies have shown that retro-commissioning commercial buildings can lead to significant energy savings - between 5% and 30%. The cost of retro-commissioning can vary between $0.10/SF to $0.60/SF. And simple paybacks can range from 3 months to 3 years, depending on the existing conditions of the facility and how much opportunity there is for improvement.
- So for example, take a 500,000 sf hospital with an EUI of 275 kbtu/sf/year with desperate need of improved operations and upgraded controls. With this example facility, we will assume there is a fairly good opportunity for retro-commissioning of the building controls. Implementing the strategies described above would yield a savings of 13-50 EUI or 6.5M-25M kBtu, and cost within the range of $50,000-$300,000.
Case Study: Wisconsin Hospital 1
Case study 1: 534,364 sf hospital in Wisconsin
This hospital was constructed in 2005. Prior to implementation, its EUI was 252, which was approximately 15% greater than the national average for hospitals and it had an energy star score of 24.
The following strategies were implemented at the facility:
- AHU SATR and static pressure reset
- Occupancy scheduling
- CHW and HW pump dP reset
- Boiler HW reset
Results
- Implementation cost - $200,000
- Annual energy savings - $143,709
- Utility energy incentive - $99,943
- Simple payback 0.82 years.
Case Study: Wisconsin Hospital 2
Case study 2: 183,060 sf hospital in Wisconsin
This hospital was constructed in 2004. Prior to implementation, its EUI was 224, which was approximately 10% greater than the national average for hospitals and it had an energy star score of 31.
The following strategies were implemented at the facility:
- AHU SATR and static pressure reset
- Occupancy scheduling
- CHW and HW pump dP reset
Results
- Implementation cost - $151,000
- Annual energy savings - $126,260
- Utility energy incentive - $78,914
- Simple payback 0.76 years.
Case Study: West Coast Hospital
Case study 3: 1.3M sf hospital on the west coast
This case study is looking at the results from an energy audit study of a large hospital on the west coast. The RCx projects have been implemented but post-project verification data was unavailable. The site was a 1.3M sf hospital with baseline EUI of 215.
The following strategies were proposed and implemented at the facility:
- BMS equipment scheduling
- Economizer optimization
- Supply air temperature setpoint reset and duct static pressure setpoint reset
- Minimum zone ventilation setpoint analysis
Results
- Projected cost: $416,500
- Projected savings: 15M kBtu / 9.8 EUI / 5.1% overall reduction
- Potential utility energy incentives: $204,000
- Simple payback: 1.5 years
Comments
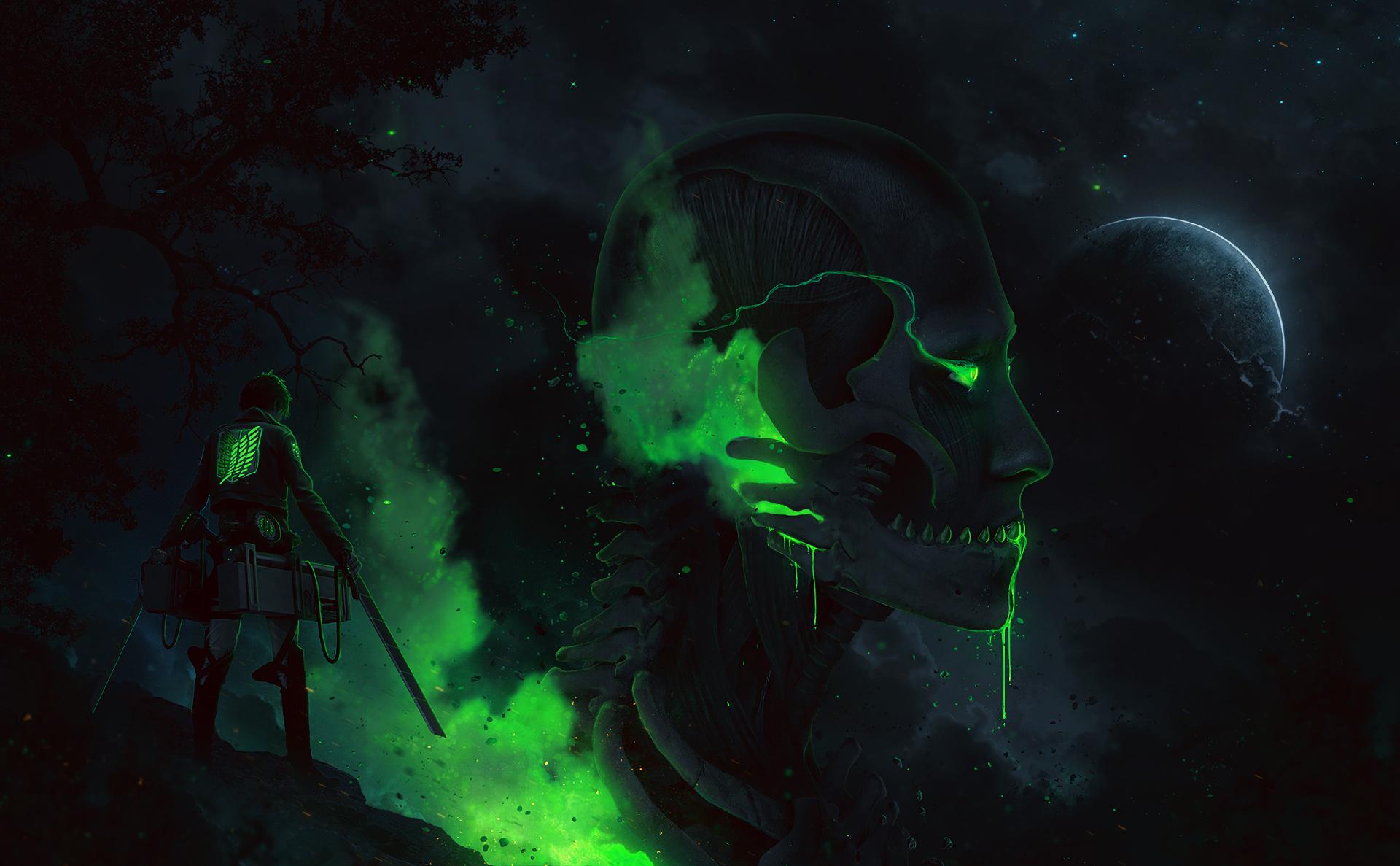
John Doe
8 seconds ago
Lorem ipsum dolor sit amet consectetur adipisicing elit. Quisquam, voluptatum. Lorem ipsum dolor sit amet consectetur adipisicing elit. Quisquam, voluptatum.
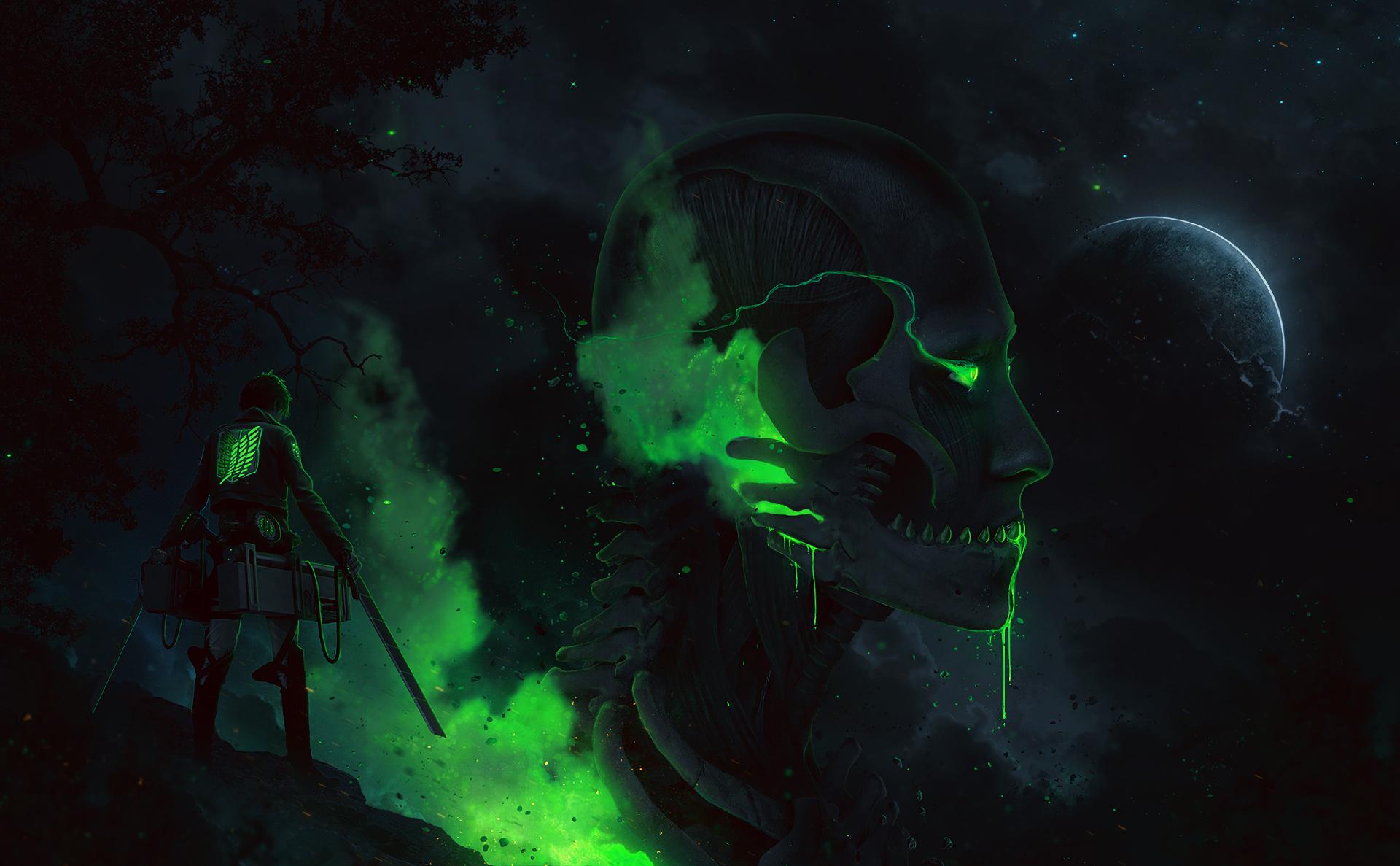
John Doe
18 seconds ago
Lorem ipsum dolor sit amet consectetur adipisicing elit. Quisquam, voluptatum. Lorem ipsum dolor sit amet consectetur adipisicing elit. Quisquam, voluptatum.