Welcome to the Decarb Guidebook
Approach
Benchmarking
Building Codes & Design Standards
State & Local Regulations
Technologies: Load Reduction
Technologies: Dehumidification
Technologies: If you must have a gas-fired boiler
Technologies: Central Plant
Technologies: Domestic Hot Water
Technologies: Steam
Technologies: Load Shifting and Energy Storage
Technologies: Emerging Technologies
Motivation Program
Pilot Projects
How to Pay for Decarbonization
Community Discussions
Workshops
Executive Summary
In traditional dehumidification scenarios, chilled water is used to condense water vapor from supply air, which is very energy intensive and requires excessive cooling and heating energy. The air is then reheated in order to maintain occupant comfort. Desiccant materials are hygroscopic — it easily absorbs water from its environment, ideal for dehumidification. By utilizing a desiccant-based dehumidification system, air can be dehumidified using 20-30% less energy.
Figure 1. Desiccant Wheel; R. Narayanan, in Clean Energy for Sustainable Development, 2017
Desiccant Systems
Technical Description
Background on relative humidity and dew point
To understand how desiccant systems work, understanding relative humidity and dehumidification is a precursor. Figure 2 shows the design outdoor dewpoint for various regions in the United States. Dew point is a function of the dry bulb temperature of air and humidity and a common design metric for medical spaces. For operating rooms, a common design setpoint is 65°F DB and 50% RH, or a dew point of 46°F.
Figure 2. ASHRAE climate zone map showing design outdoor dewpoint
Examples: For every 1,000 cfm, for an application in Atlanta, GA, this requires 6.2 gallons per hour (gph) of condensation. In Montana, 2.0 gph is required. This translates to 4.2 tons of cooling and 1.3 tons of cooling saved by using a desiccant system when compared to a traditional system that uses mechanical cooling for dehumidification. Regardless of climate zone, conditioning for hospital spaces sustainably requires innovative engineering.
How it works
Desiccant dehumidification systems cycle a water-absorbing material (such as a silica gel) through an incoming airstream. As the air passes through the system, water content is removed from the air and can then be cooled and distributed to the space. Materials used can be either solid or liquid, each with distinct advantages and are chosen depending on application. Liquid desiccant (commonly lithium chloride) offers greater controllability; however additional equipment, like a pump, is needed to circulate the liquid. Solid desiccant in the form of a desiccant wheel is a simpler system, in which a wheel is exposed to both the conditioning section and regeneration section, rotating, which circulates the absorption material. The specific desiccant material must be carefully selected based on the design conditions. The ability for the material to hold onto the water vapor is dependent on airstream dry bulb (DB) temperature and humidity.
Desiccant wheels are visually similar to enthalpy wheels, with a mesh similar to an air filter. The mesh allows air to flow through the suspended chemical desiccant. Figure 1 shows an example of a wheel and air streams utilized.
Desiccant systems require adequate velocities to allow moisture to be absorbed from the incoming air. The process has two-steps: absorption and regeneration. During absorption, the material is exposed to the airstream to be conditioned and will absorb moisture until it becomes fully saturated. With the material now saturated, it moves into the regeneration stage. This section is exposed to a warmer airstream, typically exhaust air, which causes the absorbed vapor to evaporate. On the process diagram, mixed or return air at 75 DB passes through the desiccant material and is now at the desired dewpoint. It is sensibly cooled and ready to be supplied to the space.
The dehumidification processes for a traditional over-cooling system and desiccant system are shown below on the psychrometric chart in Figure 3. Figure 3. Psychrometric chart showing the general air-conditioning process for a desiccant system
Design considerations
For new systems, custom AHU’s can be purchased with space available for a desiccant wheel. (The addition of a desiccant system occurs at the AHU, instead of at the zone level, enabling a single access point.) With thoughtful design and utilizing exhaust air, adding two wheels in series alleviates the need for additional reheat energy required for regeneration. This strategy is applicable for both return and DOAS systems.
In existing systems, desiccant systems integrate well with modular AHU’s. Energy savings will make up for additional cost from purchasing new air handling equipment. Should the engineer choose to add onto an existing air handler, there should be a bypass method in place to allow continued airflow should the desiccant system break down. This also necessitates additional cooling capacity on the coil.
Solid-form desiccant material is most commonly used, similar to the Silica Gel packets used in everything from shoes to packaged food. The same material is embedded into a wheel similar to Figure 1 and exposed to the incoming airstream.
Figure 4. Silica Gel Packets Commonly Used
Best practices
The usage of desiccant systems is largely dependent on project location. These systems would be most effective in areas with typical outdoor design RH above 50%. This includes coastal areas, especially in Southern California.
After a high number of saturation cycles, the material may need to be replaced. An appropriate maintenance plan is needed, per the specific desiccant system’s manufacturer recommendations. Many warranties last for five years, and with regular maintenance, equipment can last up to 15 years.
Although desiccant minimizes the need for additional reheat, heating coils should still be present. Regeneration air, which can be sourced from outdoors, may not allow for adequate moisture removal.
The usage of desiccant systems depends on the stringency of space humidity requirements. In California Healthcare design, these spaces are designed according to Title 24, Part 4 California Mechanical Code, Chapter 4: Ventilation, Table 4-A. Some rooms with specific humidity requirements include:
Room Type | Relative Humidity | Design Temperature |
Critical and Intensive Care | 30-60% | 70-75°F |
Delivery Room | 20-60% | 68-75°F |
Laser Eye Room | 20-60% | 70-75°F |
Newborn Intensive Care | 30-60% | 72-78°F |
Newborn/ Well Baby Nursery Suite | 30-60% | 72-78°F |
Operating Room | 20-60% | 68-75°F |
Operating/Surgical Cystoscopic Room | 20-60% | 68-75°F |
Post-Anesthesia Care Unit | 20-60% | 70-75°F |
Dehumidification is less of an issue in California, as shown by the outdoor design dewpoint map. The DoE Office of Science and Technical Information (OSTI) recognizes further exploration of alternative dehumidification systems, including desiccant systems, as a high-priority in a white-paper High Performance Healthcare Buildings: A Roadmap to Improved Energy Efficiency. This priority indicates government-level recognition of the benefits of desiccant systems and, thus, the need to further explore it. This could lead to funding opportunities for pilot facilities, which could subsidize the cost of installing desiccant systems into healthcare facilities.
Desiccant DOAS for Low Temperature Spaces
Where desiccant systems are used, they are best incorporated into a Dedicated Outdoor Air System (DOAS), so that only outdoor air, the primary source of moisture, is treated through the desiccant. This reduces energy for dehumidification and re-cooling, compared to a mixed-air desiccant system, but also reduces the size of the desiccant wheel. Refer to the Guidebook chapter on DOAS for more information about DOAS in general.
Desiccant systems can also use exhaust air for recharge of the desiccant. Desiccants operate from a difference in relative humidity. When high-RH outdoor air passes through one side of a desiccant wheel, the airstream on the other side must be lower RH in order to remove moisture. The RH difference between the airstreams can be increased by:
- Lowering the temperature of the outside air. Lowering temperature raises RH. In many cases, the system will precool outside air, removing moisture and leaving the air saturated.
- Raising the temperature of the ren=generation air. Raising temperature lowers RH.
- Use a dry airstream for regeneration. Discharge exhaust or relief air from the conditoned space (air that must be removed anyway, to achieve the outside air ventilation requirement) can be routed through the regeneration side of the desiccant wheel. The relief air is cool and dry. Even if it has to be heated some to get the required dehumidification, it is cooler and drier, requiring less heat and adding less heat to the outside air flow.
- A combination of the above.
Below, figure 5, shows a system diagram for a desiccant-based DOAS for a surgery suite. The operating room design condition is 65F DB at less than 55% RH - 48F dewpoint. The desiccant wheel easily accomplishes the task, drying outside air to a dewpoint of 42 before mixing with return air.
Figure 5: System and psychrometric process diagram for DOAS with desiccant wheel and exhaust air regeneration
How does this decarbonize?
Since the air isn't subcooled, the need for both cooling and reheat decreases, saving energy at the chiller and boiler. Reduction in boiler capacity can reduce Scope 1 Natural Gas emissions by 10-20%, and reduction in chiller load reduces Scope 2 Purchased Electricity by the same amount. For hospitals with a large proportion of humidity-controlled spaces, such as ORs, this number is even greater.
Implementation
Barriers: Culture
Healthcare engineers prefer traditional design practices and technology and since this may be an unusual system for engineers and maintenance personnel, there may be some resistance to implementing a desiccant system. Educating facility staff with some additional training may be required for proper operation and maintenance.
Barriers: Technical
The current desiccant system technology degrades in effectiveness and absorption capacity relatively quickly. This depends on the amount of airflow and moisture content. This would be another component to replace on a similar frequency as air filters, which follow a five-year maintenance schedule.
The regeneration cycle requires a supply of hot and dry air, which could require heating of exhaust air used. Temperate exhaust air can be used; however, lower airflow rates are achievable for warmer regeneration air, enabling the use of waste heat. This will have to be taken into consideration during the design process.
Strategy
There are a few key points to take note of when designing a desiccant system. Using exhaust air heat recovery can decrease the need for additional heating during the regeneration process. Conducting a basic energy analysis for the intended building helps determine the proportion of reheat in relation to the total energy load. If the energy required for air-cooling and additional reheat exceeds 60%, a desiccant system may be a suitable option. Also, it is advisable to adhere to the system's manufacturer guidance regarding operating setpoints, as systems can vary. Lastly, the energy savings can be calculated by considering the required cooling capacity using the manufacturer-specified operating conditions.
Financial analysis and business case
Similar in cost to the addition of an enthalpy wheel energy recovery system. Depending on the desiccant system selected (whether solid or liquid), the additional equipment will be a minor addition. The energy savings will cover the cost within a single year. In extreme cases, the desiccant system may remove the need for a separate subcooling chiller entirely, which will considerably save upfront and operating costs.
Case Study: Atlanta Hospital
ATL GA Hospital
During the design phase for a hospital in Atlanta, Georgia, the design team conducted a simplified energy analysis, comparing energy and cost savings between numerous systems, including numerous configurations of an AHU outfitted with a solid-desiccant wheel. The most efficient configuration, which utilized exhaust air heat for regeneration, used 90% less total energy than a typical mixed-air system w/ subcooling and was 90% cheaper to operate on an annual basis.
Case Study: CA Hospital
We need a case study for use of desiccant systems in a California hospital! If you have information that we could publish here, please comment on this page or let us know.
Comments
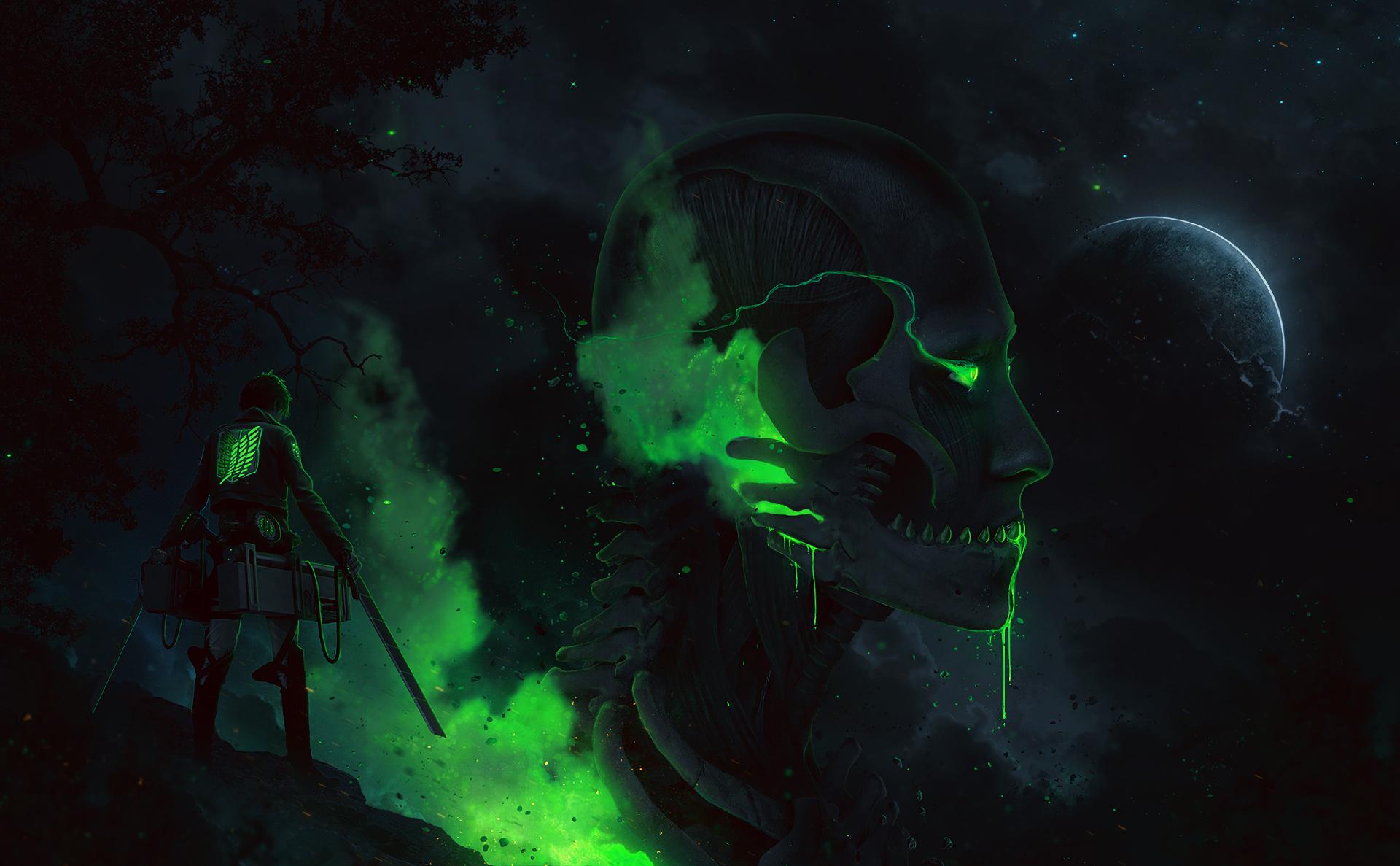
John Doe
8 seconds ago
Lorem ipsum dolor sit amet consectetur adipisicing elit. Quisquam, voluptatum. Lorem ipsum dolor sit amet consectetur adipisicing elit. Quisquam, voluptatum.
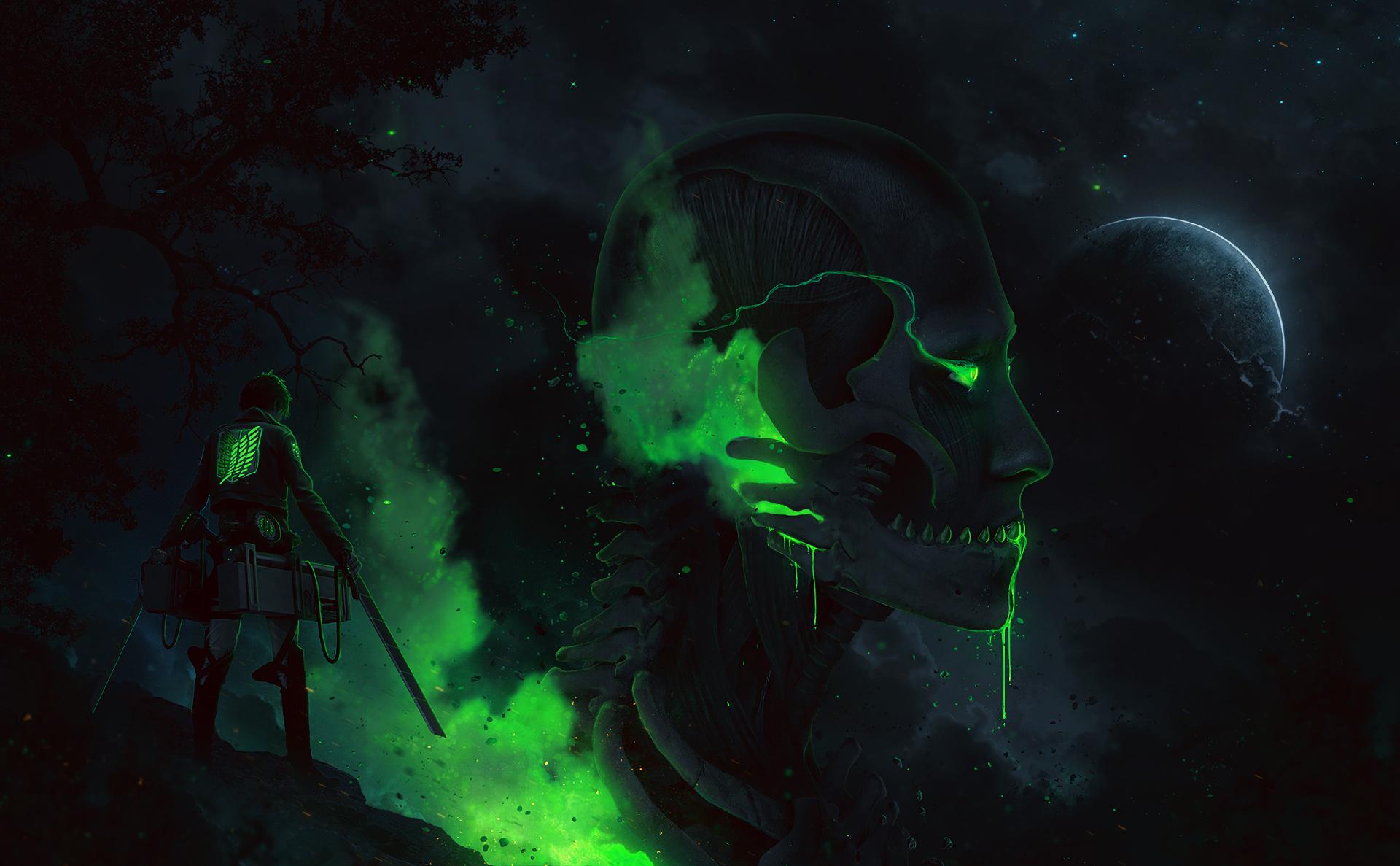
John Doe
18 seconds ago
Lorem ipsum dolor sit amet consectetur adipisicing elit. Quisquam, voluptatum. Lorem ipsum dolor sit amet consectetur adipisicing elit. Quisquam, voluptatum.