Welcome to the Decarb Guidebook
Approach
Benchmarking
Building Codes & Design Standards
State & Local Regulations
Technologies: Load Reduction
Technologies: Dehumidification
Technologies: If you must have a gas-fired boiler
Technologies: Central Plant
Technologies: Domestic Hot Water
Technologies: Steam
Technologies: Load Shifting and Energy Storage
Technologies: Emerging Technologies
Motivation Program
Pilot Projects
How to Pay for Decarbonization
Community Discussions
Workshops
Executive Summary
Gas-fired water boilers are used in hospitals to provide hot water for building heating and domestic hot water use. The combustion efficiencies of traditional boilers are 80% or lower. Improvement in the combustion efficiency can help to maximize the input energy supplied.
A technology worth considering is the implementation of condensing boilers. It is documented that condensing boilers operate at combustion efficiency of 90-95% in a system with low return water temperatures, which can use less natural gas to produce the same output. In order to achieve a higher efficiency, the system will need to be redesigned to achieve the conditions where high efficiency occurs, including using lower supply temperatures. It is crucial to redesign the entire system from the start and ensure there are adequate controls and proper equipment sizes being used.
While this technology can improve the efficiency of the boiler plant and reduce natural gas consumption of a facility, it is fairly limited in its overall impact on carbon emissions in that it still relies on the combustion of natural gas to produce heat. This should be considered an interim step in the overall decarbonization process.
Condensing Boilers
Technical Description
How it works
A traditional boiler is a casing which includes a heating chamber. Natural gas is piped to this chamber and ignited to burn the gas. The burned gas provides byproducts, chemical elements, such as carbon dioxide, hydrogen and oxygen and heat. This heat is transferred to cold water pipes inside the boiler through an internal heat exchanger to transmit heat via an inline hot water heating pump to heating coils in air terminal boxes, fan coil units, or air handling preheat coils. The byproducts are exhausted from the boiler through the flue. This flue is superheated and that heat is exhausted out of the building. In traditional boilers, the heat, otherwise known as energy, is exhausted to the atmosphere and considered waste heat.
The difference between a traditional boiler and a condensing boiler is how the byproduct is handled. Instead of that waste heat being exhausted to the outdoors, it is captured and added to the incoming water to increase the temperature of the feed water to the boiler. This allows the boiler to operate at a smaller delta T, or temperature difference between return and supply water temperatures. This process increases the combustion efficiency of condensing boilers. The waste heat is captured and reused which reduces the amount of input energy needed. The efficiency of a traditional boiler is at best 80% whereas a condensing boiler can be 90-95% efficient.
Design Considerations
Condensing boilers require additional parts to maximize the extraction of heat as follows:
The condensing system will require a larger heat exchanger surface area to extract heat energy from the flue gases. It is critical that a high-grade stainless steel be used in this heat exchanger. When the hot gas temperature is decreased, it will condense into liquid, which is acidic and corrosive. Without a high-grade stainless steel, this liquid could erode the heat exchanger or flue material over time.
The system will also require the installation of a neutralizer tank to address boiler drainage. The purpose of this condensate neutralizer is to filter and neutralize water by-products before dispensing down the drain.
Control Strategies
Typically when selecting condensing boilers, you want a variable primary or (if large enough) a variable primary, variable secondary pumping system. With variable primary flow systems, minimum pressure or flow requirements are usually required at the boilers. This means a 3-way bypass valve will need to be introduced on the main heating hot water (HHW) pipe to recirculate water if the secondary flow requirement is lower.
In order to accomplish the above and get to the higher level of efficiency, a hot water reset strategy is needed. Let’s say, for example, the base system is sized for a 150℉ supply water temperature and a 120℉ return temperature loop, otherwise known as a 150-120℉ loop for the peak winter design, but in the summer that system can run down at a 130-100℉ loop. The hot water reset strategy can utilize a trim and response sequence based on either variable air volume (VAV) box heat output values or HHW valve position feedback values.
The goal of the trim and response sequence is to gradually lower the HHW supply temperature towards a minimum point based on feedback for actual demand for hot water in the building. This sequence typically operates more in the shoulder seasons or the summer when the need for heat is much less. A good resource for specific examples and details for the trim and response sequence can be found in ASHRAE Guideline 36.
Advantages
Energy efficiency
Recovering waste heat from the boiler flue improves the efficiency of the condensing boiler by preheating the feed water. This process reduces the amount of natural gas consumed by the boiler to meet the heating load.
Boiler turndown
Condenser boilers operate with a high turndown ratio, which provides the ability to meet heating load demands. The use of multiple boilers operating at low firing rate allows the overall plant to operate at a higher efficiency.
Best Practices
To gain the efficiency benefits, the heating system must be based on condensing temperatures. The condensing boiler system return water temperature must be below the dewpoint of the boiler exhaust, ideally around 80℉ or lower for optimizing the system. See below efficiency curves based on ANSI Standard Z21.13 testing and rates of condensing boiler performance.
Figure 1. Typical Condensing Boiler Efficiency Curves [1]
Additional recommendations include:
- Install a boiler management system dedicated to control and monitor boiler operations. This will provide the ability to operate multiple boilers at a lower firing rating to meet present loads and improve efficiency.
- Individual boiler flue is recommended instead of a combined flue for multiple boilers. The individual flue allows for variability of airflows and will require a fan to remove combustion products out of the building.
- Condensate drains are needed at the bottom of the flue stack, and a heat exchanger with condensate trap. Drain(s) to be directed to a neutralized tank before going to drain. Coordinate with plumbing engineer for material compatibility.
- Lower return water temperatures to the boiler improve the efficiency. Design the system to the lowest possible hot water supply temperature, for example, 140℉, for ASHRAE Climate zone 3C.
- Larger heating coil requirements: Larger and more row coils, to maximize surface area will be required with lower hot water supply temperature. Be mindful of water and air pressure drop through these coils and must be accounted for in fan and pump pressure drop calculations.
- Recommend to install variable primary pumps in condensing boiler systems, as opposed to two variable primary and two secondary pumps, which will lower the installation and operating cost.
- Designers should be wary that oversizing boilers, short-cycling, and poor operational control can eliminate any efficiency gains in the system.
How does this decarbonize?
Replacing traditional boilers with condensing boilers will not completely eliminate the GHG emissions from the boiler plant, but it will improve the overall efficiency by recovering waste heat. When waste heat is recovered from the boiler flue, it reduces the amount of natural gas that is consumed by the boilers to meet the same heating output. Less natural gas burned means less Scope 1 Stationary combustion emissions.
However, this technology is fairly limited in its overall impact on carbon emissions in that it still relies on the combustion of natural gas to produce heat. This should be considered an interim step in the overall decarbonization process.
Implementation
Increasing the thermal efficiency of a condensing boiler requires a return water temperature less than 130℉. Most heating systems have return water temperatures much higher than 130℉. Existing heating coil selections are based on higher supply water temperature and smaller temperature difference, approximately 30-40℉. To achieve similar results with a condensing boiler compared to a conventional boiler, this would require an increase in the surface area of the coil. This may pose a challenge in retrofitting existing heating systems.
Barriers: Codes
Currently, the Title 24, Part 6, California Energy Code does not include any reference to condensing boiler equipment. This is not included in the Table 110.2-K for minimum efficiency requirements. As a result, it's often overlooked during design and equipment specification.
Note: recent energy code legislation in the state of WA requires high-efficiency boilers, which effectively requires condensing technology.
It is recommended that condensing boilers be included in the Table 110.2-K for minimum efficiency requirements in the next code cycle. It is easy to implement this technology in new construction, but retrofit projects in existing buildings may have some challenges in dealing with existing equipment.
Hot water systems are typically based on 180-200℉ with return temperatures being too high for what is needed for condensing boilers.
Reheat coil selection will also need to be taken into account since traditional coils are often sized for higher temperatures.
Barriers: Technology
Boiler Oversizing / Low Temperature Difference (delta T)
Condensing boilers rely on lower entering water temperatures, less than 130℉, in order to achieve their efficient operations. The problem of oversizing, particularly for low-load conditions, is chronic in design engineering (most recent source) [2] (source) [3] (another source) [4]. If the boiler sizing results in cycling, the system efficiency losses outweigh the equipment efficiency gains.
If boilers cycle, there are natural gas losses associated with the starting and stopping of the boiler. One manufacturer estimated these losses as high as 25% of the boiler nameplate (e.g. A 1,000,000 BTU boiler uses 250,000 BTU each time it cycles off and on). If the boiler were to cycle off and on four times in an hour, the full nameplate of 1,000,000 BTU would be lost).
Since 25% seems very high, a lower number, such as 5% might be a better assumption (e.g. A 1,000,000 BTU boiler uses 50,000 BTU each time it cycles off and on). If the boiler were to cycle off and on four times in an hour, the full nameplate of 1,000,000 BTU would be lost every 5 hours.)
A Kaiser Permanente white paper [5], issued to design engineers, recommends the following as minimum checksums for boiler sizing:
For day clinics (medical office buildings) boilers should be capable of efficient operation at loads of 0.5 BTU/ft2.
For hospitals, boilers should be capable of efficient operation at loads of 5 BTU/ft2.
Natural gas heating system efficiency may be effectively unrelated to the boiler equipment efficiency. A measurement and verification study of condensing boilers [6] installed at a facility in 2018 showed that the overall system efficiency was 35% during the winter months, even though the specified efficiency of the boilers themselves was 90%.
Boiler oversizing leads to poor supply water temperature control, and low delta T syndrome.
In a M&V study of condensing boilers in actual operation [7], the supply water temperature control showed a standard deviation of +/-13.5℉.
In the same M&V report, the design Delta T was 25℉, which was never achieved. A significant portion of observations had delta T less than 10℉.
This technology does have some drawbacks and may present challenges to implement. To maximize the potential condenser boiler efficiency, it is critical to have the return water temperature at less than 130℉. This can pose a challenge to renovation in an existing system. The original heating coil selections are usually based on a hot water supply temperature, say 180℉ with a temperature difference of 40℉. Simply replacing the existing traditional boiler with a condensing boiler does not maximize the thermal efficiency. The change to the heating coils is required to maximize thermal efficiencies. The supply water temperature for a condensing boiler would be based on approximately 140℉, and revised coil selection would be required to meet existing heating load with the revised hot water setpoint 140℉.
Barriers: Culture
Many practicing engineers do not design condensing systems well. Engineers are familiar with this technology, only as represented by manufacturer literature.
Based on ongoing CEC research [8], a study called Quantifying Energy Losses in Hot Water Reheat Systems indicates that most buildings in California spend the majority of the year at very part load conditions, which suggest more consideration should be made to part load performance – the strategy goes beyond just specifying a condensing boiler.
Figure 2. Among buildings with condensing boilers, less than half are actually operating at condensing temperatures
Figure 3. Corresponding return water temperatures
Evidently, significant education to the design community is needed.
Strategy
To implement this technology, it is recommended to evaluate the existing heating hot water requirement, with an emphasis on the actual low-load needs.
Assess whether the reduction in supply water temperature has any impact on the overall comfort of the building.
This can be achieved by adjusting supply water temperature incrementally over time, and documenting indoor conditions.
If the building can function with the supply water temperature at 130℉, this building could be considered for using condensing boiler(s).
The lower the return water temperature the better combustion efficiency can be obtained.
Financial analysis and business case
Decarb Healthcare is looking for project cost estimates for a condensing boiler project to use as a sample. If you have a project and are willing to share the information please reach out to us at [email protected].
Case Study: Kaiser Roseville
Kaiser Hospital - Roseville, California.
Kaiser Hospital completed a conversion from a traditional, non-condensing boiler to a condensing boiler. In correspondence with the building engineer at the time, several questions were submitted for responses based on real life experience. The questions and responses are as follows from a Building Engineer at Kaiser Roseville CA:
Why did you change from traditional boiler setup to condensing boiler system?
“Primarily for energy savings. The primary heating source is a cogen system that provided a substantial amount of the required heating hot water. The building engineers found that the larger gas-fired boilers cycled on/off frequently in low load conditions.”
What changes were required to accommodate the condensing boiler system?
“Standard pipe configurations and flue gas modifications.”
What challenges were faced with this implementation? How were these challenges overcome?
“The burner blowers prefer a clean source of make-up air. A disposable pre filter was added to the intake location. The modules (boilers) need to operate as designed, without outside control system interface. Their internal programming does a good job of staging modules as load conditions change.”
“Avoid prolonged shutdowns of the modules to avoid seals drying out and cracking.”
Are you satisfied with the results, and what specific improvements have you seen?
“The Riello boilers (condensing boiler product) seemed to perform well after the operators became familiar with the system. Allowing the system to run as designed makes a big difference in continued operational success. Personally, not having to run larger Cleaver Brooks boiler (non-condensing boiler product) to maintain the heating hot water (HHW) loop temps on moderate days give you peace of mind that energy is being saved.”
Would you recommend this conversion from non- condensing to condensing boilers?
“I would recommend them (condensing boilers) for a number of reasons such as; light load conditions, space constraints, and energy savings. In addition, I would recommend a service agreement for the first year of operation, to allow the plant operators and mechanics to learn and become proficient in the care and use of the system.”
M&V outcomes:
The Roseville Medical Center currently has a 12-month EUI of 209. 59.6% of that is natural gas, which is a Natural Gas EUI of 124.4 kBTU/sf-yr.
Comments
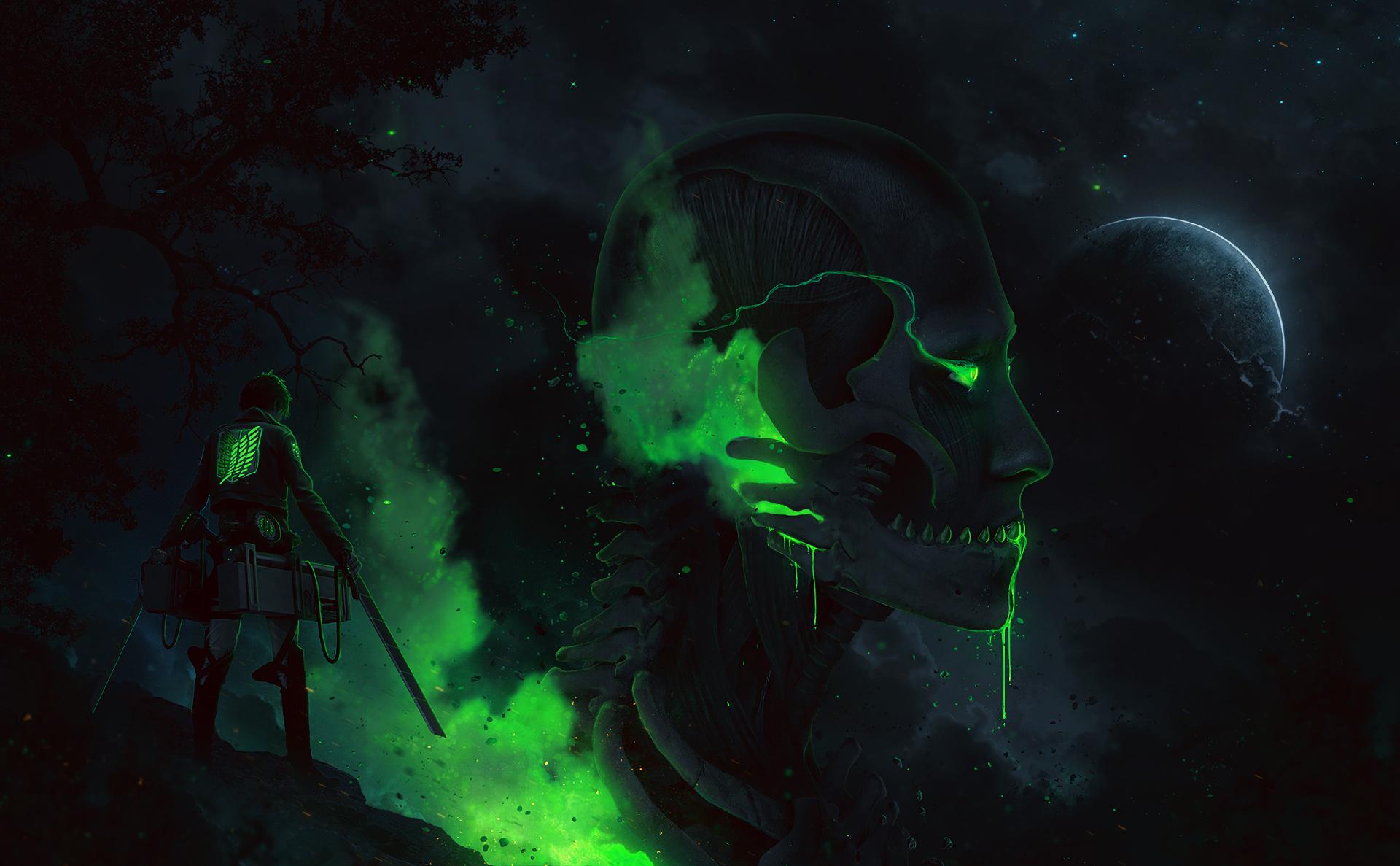
John Doe
8 seconds ago
Lorem ipsum dolor sit amet consectetur adipisicing elit. Quisquam, voluptatum. Lorem ipsum dolor sit amet consectetur adipisicing elit. Quisquam, voluptatum.
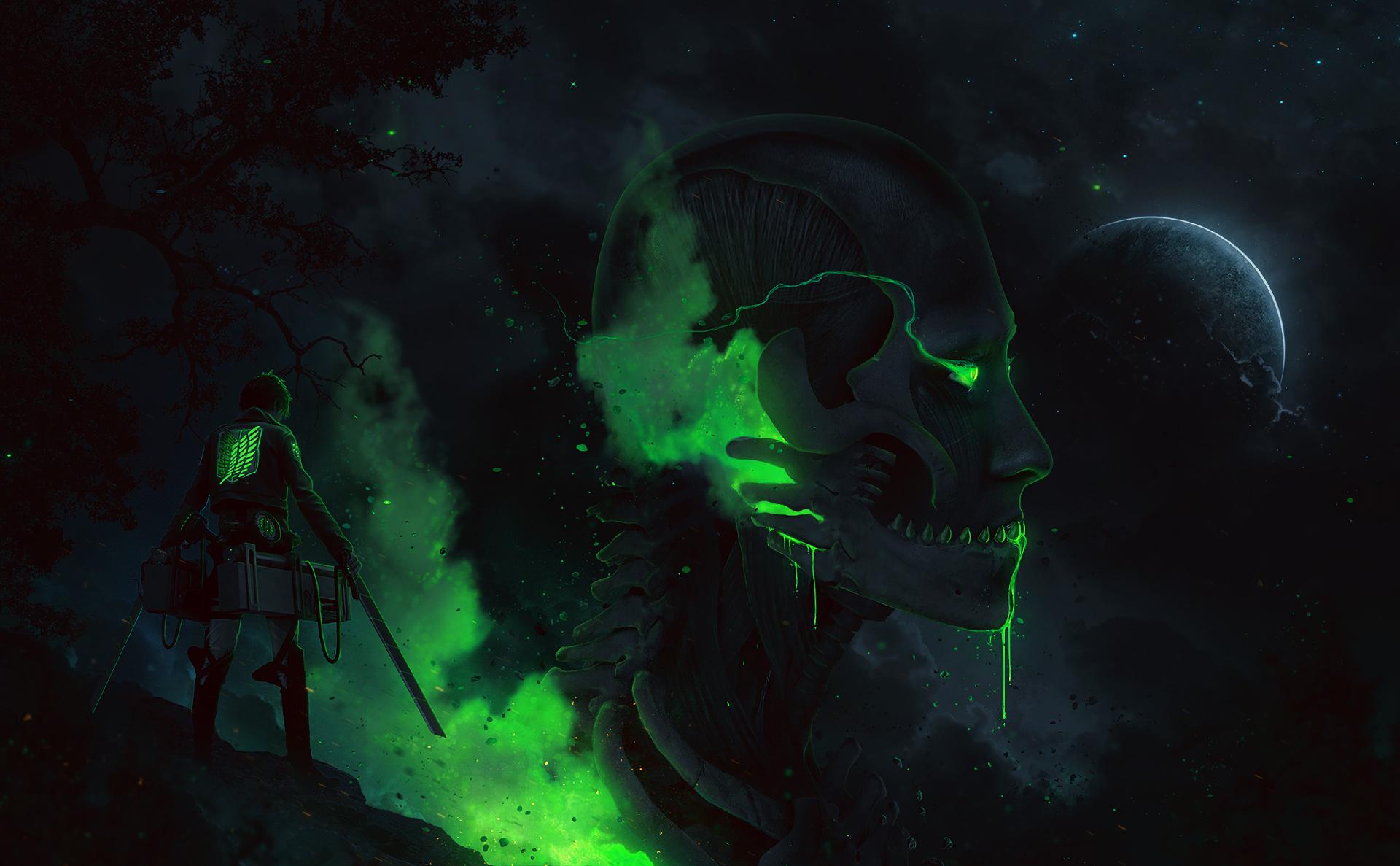
John Doe
18 seconds ago
Lorem ipsum dolor sit amet consectetur adipisicing elit. Quisquam, voluptatum. Lorem ipsum dolor sit amet consectetur adipisicing elit. Quisquam, voluptatum.