Welcome to the Decarb Guidebook
Approach
Benchmarking
Building Codes & Design Standards
State & Local Regulations
Technologies: Load Reduction
Technologies: Dehumidification
Technologies: If you must have a gas-fired boiler
Technologies: Central Plant
Technologies: Domestic Hot Water
Technologies: Steam
Technologies: Load Shifting and Energy Storage
Technologies: Emerging Technologies
Motivation Program
Pilot Projects
How to Pay for Decarbonization
Community Discussions
Workshops
Executive Summary
Hospitals commonly use natural gas-fired boiler systems to produce steam for sterilization and humidification. Alternative non-natural gas options to generate steam include: (1) Electric steam generators and (2) concentrating solar collectors. The Guidebook will catalog and explain the non-fossil fuel technologies and explore alternative methods of generating steam.
Alternative Steam Generation Methods for Sterilization and Humidification
Technical Description
Traditional Steam Use Background
The humidification and sterilization loads drive the need for steam in a hospital. Sterilization is a crucial process in hospitals, especially in central sterile areas where medical equipment and devices are brought to be cleaned and sterilized for re-use. Sterilization is the last step in cleaning and disinfecting instruments for use - it kills all microorganisms left on the equipment. This process is done in an autoclave where the equipment is exposed to direct steam at a required temperature and pressure for a set amount of time. Each piece of equipment has a specified exposure time and temperature as specified by the manufacturer and depends on the type or material of the item, whether the item is unwrapped or wrapped, and the sterilizer type. Typical steam sterilization temperatures are 250°F or 270°F, set by the manufacturer and aligns with existing standards and guidelines. For wrapped healthcare supplies, a minimum exposure period for sterilization is 30 minutes at 250°F in a gravity displacement sterilizer or 4 minutes at 270°F in a pre-vacuum sterilizer. Dry saturated steam, not superheated steam, is needed for proper moisture control and the ideal pressure from steam sterilizers at the source is 30 to 35 psig; however, the pressure should not be more than twice the chamber pressure at the desired temperature.
Maintaining an appropriate relative humidity is necessary for occupant comfort, protecting electronic equipment, and preventing hospital acquired infections (HAI). In a hospital, certain spaces have strict relative humidity (RH) requirements. For example, according to Table 4-A in the California Mechanical Code, the post-anesthesia care units (PACUs), operating rooms, patient rooms, and procedure rooms, all must maintain an RH level between 20-60 percent. Critical care and intensive care rooms and newborn intensive care spaces must maintain an RH between 30-60 percent. Additionally, spaces associated with the pharmacy must maintain an RH below 60 percent.
These processes require steam. Designers need to find a way to produce 270°F steam in a hospital, and to achieve this without natural gas boilers, the design must rely on electricity or other renewable energy sources to generate steam. In many cases, the steam also must be piped to other parts of the hospital or campus after being generated at the boiler plant, leading to more energy losses.
Alternative steam generation options
Because hospitals need steam for sterilization and maintaining strict humidification requirements, boilers and steam piping systems realistically cannot be completely eliminated in order to reduce a facility’s carbon footprint. However, there are several alternative steam generation methods that can still reduce GHG emissions including electric steam generators and concentrating solar collectors.
Electric Steam Generators - Sterilization
Electric boilers are used as steam generators for a steam sterilizer or autoclave. They are easily integrated into a system since they can be located wherever power is accessible. In this way, electric steam generators can be used to bypass house steam to provide steam closer to the point of use.
An integral boiler or a remote boiler method can be used. An integral boiler sits under the footprint of the autoclave for direct transfer of steam but is limited to 45 kW of power. For larger autoclaves (24x36x60”), a remote boiler would be more powerful. They also take up more space so may be located outside the room or next to the autoclave. Both of these methods would require 3-phase power to be available near the autoclave.
When the design for a building is using a house steam system, the electric steam generator for the house system can be used for sterilization if it is already producing steam at greater than 50 psi. The steam is then piped from the electric steam generator to the sterilizers in the hospital. The electric boilers, as described previously, allow the steam generation to happen at the point of use.
Electric Steam Generators - Humidification
Electric steam generators are an alternative to steam boilers that eliminate the need for natural gas. Instead of burning combustible fuel (i.e. NG) to boil water and convert it into steam, electric steam generators submerge heating elements in water in a pressurized vessel to create steam. The vessel creating steam is shown below in Figure 1. They are smaller and more energy efficient than natural gas boilers because of the lack of extensive piping systems. Electric steam generators also require less maintenance and have longer lifespans. Additionally, because natural gas is flammable, the fuel line must be inspected and maintained regularly. Electric steam generators are 100 percent efficient because all of the electricity is used to turn water into steam, while natural gas boilers typically achieve 80-95 percent efficiency at most. When they are not in use, electric steam generators can be turned off whereas regular boilers continue to burn fuel even when there is no demand for steam. Going electric does require an addition to the electrical infrastructure which may require an increase in emergency power since many spaces still need to be operable if the power were to go out.
Figure 1. Electric steam generator installed in a San Francisco hospital.
Typical sizes of gas-fired humidifiers, according to DriSteem, range from 50 to 600 lbs/br. Typical sizes of electric steam humidifiers range from 5 to 324 lb/hr and can be located in the air handling unit or in the ducts at their point of use. These electric humidifier units can be linked together to provide up to 4,560 lbs/hr. They can also have tighter controls than gas-fired humidifiers with as close as within 1 percent set point when using an electric resistive element.
There are two types of electric steam generators: electrode type and ionic bed type. The electrode type passes an electric current through the water to create steam, which makes the quality of the water important. Replacement or cleaning of the tank will depend on the quality of the water and may require frequent draining, filling, and reheating which may not be acceptable for some critical applications. As a result, electrode technology has higher maintenance costs than ionic bed type and cannot provide continuous operation or tight control. The ionic bed type uses resistance heating elements to boil water and humidify the air, but any quality water can be used. Maintenance is simpler for this type because the bed can be replaced. In either case, the humidification will need to be paused for maintenance which could be a monthly or quarterly commitment, and may be an issue for more critical humidification applications. Depending on which type is chosen, the facility will need to have the ability to treat the water. Using reverse osmosis deionization (RO/DI) water will provide tight control with minimal maintenance since it will not need draining or skimming.
Concentrating Solar Collectors
Concentrating solar collectors use an area that captures the solar radiation that is much greater than the absorber area to turn direct solar radiation into heat. The concentrating solar collector takes the heat from the sun, reflects it with a mirror, then focuses the heat on one area filled with water to generate very high temperatures in the production of steam. For an industrial power plant covering large areas, this steam is typically then sent through a power system, and used to generate electricity.
Figure 2: Example of parabolic trough solar collectors from the Department of Energy. Heats the fluid in the absorber pipe to a high temperature
Types of concentrating collectors include parabolic troughs, compound parabolic, fixed reflector moving receiver, fixed receiver moving reflector, Fresnel lens, and central receiver. Figure 2 shows an example of a parabolic trough collector which can be used with a sun tracking device to produce water with a temperature of 480-750F. For a solar-thermal power plant, a typical solar collector field contains many rows but one collector module is typically 15-20 feet tall and 300-450 feet long. Below in Figure 3 is a common concentrating solar power system. Usually the collector fields are larger than 100 MW but can usually get 5 to 10 MW of power per acre. Smaller concentrating solar collectors can also be used directly where power is needed such as with dish/engine systems that can produce 5 to 25 kW of power per dish.
Figure 3. A parabolic trough collector generates steam which powers a turbine to create electricity. This is a common concentrating solar power system.
While a solar thermal power plant uses the steam to power a turbine which generates electricity, other industries use the steam for a variety of other needs. The steam can be used for industrial applications such as water desalination, enhanced oil recovery, food processing, chemical production, and mineral processing. For example, in the processing of pistachios, steam at 480F is used to pasteurize, blanch, and roast the nuts. A 2.3 MW solar field was created in Madera, California for this purpose and configured as shown in Figure 4. Currently there are not many applications of solar thermal concentrator technology being used to directly generate steam for humidification, but based on the temperatures and pressures required by hospitals and what is being generated for these other industrial processes, it seems within the realm of possibility.
Figure 4. Sunlight heats a working fluid that then is used to boil water which heats, dries, and cleans foods. Because the system goes from sunlight to steam instead of sunlight to steam to electricity to steam, the energy losses are reduced.
The areas in the US that have the highest solar radiation are shown in Figure 5 as being primarily in the Southwest. Concentrating collector systems are best used in areas with more than 2,500 annual sunshine hours which is mostly in the Southwest and parts of southern California as shown in red and dark red.
Figure 5. Direct Solar Irradiance required for concentrating solar collectors.
For sterilization which is accomplished through an autoclave, solar concentrators can be paired to provide the steam, as shown below in Figure 6. A review was conducted of solar thermal collectors for sterilization and discovered that not many working installations exist but there are numerous prototypes. For rural health centers that do not have access to electricity, solar thermal collectors used with autoclaves or pressure cookers that sterilize medical equipment have been used on a smaller scale. There have been multiple successful prototypes that achieve proper sterilization of equipment, mostly for use in underserved, off-grid communities. According to MIT News, a research team was able to generate steam with a solar collector of about 2 sq meters to power a small clinic autoclave. One vessel reached the maximum temperature of 270°C and pressure of 15 psi for more than 15 minutes which is required for sterilization.
Figure 6. Ways to pair a solar collector with an autoclave.
Non-concentrating solar collectors, where the area that captures the energy is the same size as the absorbing area, require global solar radiation, which includes scattered and direct solar radiation, as shown in Figure 7. The most advantageous areas are the red and dark red areas. The flat plate collector and the evacuated tube collector are the non-concentrating solar collector technologies.
Figure 7. Global Horizontal Irradiance used by flat plate solar collectors.
Flat plate collectors use copper tubes with a heat transfer fluid going through an insulated box with an absorber surface and thermal insulation to prevent heat loss. They are used in low heat applications usually with current designs generating temperatures up to 212°F but more advanced designs with ultra-high vacuums can provide temperatures up to 400°F. Evacuated tube collectors are rows of glass tubes, as shown in Figure 8, each of which has a heat pipe collector inside with a heat transfer fluid in a vacuum. Currently, they generate temperatures of up to 260°F but a few more advanced designs can generate temperatures of up to 480°F. [1]
Figure 8. SunQuest 250 using evacuated tubes with a coating to attract UV rays.
These collectors fit best on the roof of a building oriented toward the sun or integrated into the façade. There are not many large companies that sell these technologies, so the majority of these systems are manufactured by small to medium sized companies. Applications include swimming pool heating, water heaters, agricultural drying, desalination, and space heating.
Non-concentrating solar collectors can also be used to pre-heat the make-up water before the boiler. The preheated water can also be added to the return loop before it goes back into the steam boiler. The use of a hot water storage tank provides a backup battery where water could be heated during the day to 180-190°F and stored, then a mixing valve could be used to extend the hours.
How does this decarbonize?
Because the sterilization and humidification processes require steam, the traditional way of generating that steam is through methane gas fired boilers. The alternatives described above use electricity or renewable energy to generate steam which reduces the need to combust fossil fuels in the facility. Methane gas fired boilers are typically up to 80-90 percent efficient which means nearly 20 percent of the site energy is wasted in the process. There are additional losses in the distribution and transmission of that methane gas which makes the wasted source energy even greater. Electric steam generators, on the other hand, are essentially 100 percent efficient. The carbon intensity of systems using electricity is dependent on the emissions factor of the utility providing the power. Electrifying steam generators remove Scope 1 emissions from the facility. There will be increased Scope 2 emissions, however. Scope 2 purchased electricity emissions always have the opportunity to be net zero.
Replacing gas fired steam boilers with a concentrating solar collector could reduce or eliminate Scope 1 Natural Gas emissions completely since the system is using renewable energy. If the solar collector is not large enough to generate the amount of steam needed, it will, at a minimum, preheat the feed water and reduce the amount of additional non-renewable energy needed to produce the steam. An option not discussed in detail above is using a concentrating solar collector system as a source of power. A concentrating solar collector system could be paired with an electric steam generator to produce steam without the use of direct on-site combustion of fossil fuels, effectively eliminating the Scope 1 emissions for steam production.
Implementation
Electric Steam Generators
Barriers: Cost
Because gas is typically less expensive than electricity in most locations, the operating cost of the electric humidification system is much higher than that of a natural or LP gas humidification system. However, gas systems require flue venting and some require a sealed combustion air supply which may make the installation of a gas powered system more complicated.
The lifetime of equipment specified for hospitals is typically 30 to 40 years. In this way, it is important to consider the life-cycle cost of the system with future natural gas prices in mind. According to the US Energy Information Administration, the price of natural gas, crude oil, and propane prices for heating and cooling are expected to continue to rise rapidly. In 2020, the cost of natural gas was 2.49 $/MMBtu while in 2020, the prediction is 4.26 $/MMBtu and over $7 by 2050.
Solar thermal collectors
Barriers: Policy
The Investment Tax Credit (ITC), which is a policy mechanism to support the growth of solar energy in the US, is currently a 26 percent federal tax credit claimed against the tax liability of residential and commercial and utility investors in solar energy property for projects that begin construction in 2021 and 2022. This then steps down to 22 percent for projects that begin construction in 2023, and then again to a permanent 10 percent after 2023.
Solar thermal technologies could be better supported by the state and federal government through policies that include tax credits, research and development efforts, and renewable thermal portfolio standards. Other examples of assistance that may help to introduce more solar thermal technologies could be through clean energy funds and low-interest loans. If solar thermal technology was being used to generate electricity instead of steam, the DOE is working to reduce the cost of utility-scale solar and create financial incentives through Solar Renewable Energy Credits (SRECs).
Barriers: Culture
According to the Renewable Thermal Collective, the main barrier to implementation of solar thermal collectors is that there aren’t many projects that have used it before, so there is a lack of information. There are existing knowledge gaps in buyers around solar thermal technologies’ capabilities, complexities, space requirements, potential heat output, and costs.
Barriers: Technology
While it seems solar thermal collectors may need to be developed more to produce steam for hospital applications, they are ready to use for producing heating hot water. A solar thermal collector can easily integrate at multiple points in an existing steam system or heating hot water system to improve the efficiency of the process.
To understand the size of the system needed, let’s explore the following example, while keeping in mind that the humidification needs will depend greatly on the outdoor conditions and type of systems used. A large hospital in San Francisco may require about 4,000 pounds per hour of steam for humidification (4,160,000 Btu/hr) and has a surface area on the roof of approximately 36,000 sq ft. The Mojave Solar Project generates a nominal 250 MW on 1,764 acres of land which is approximately 3.25 Watt/Sqft or about 11 Btu/hr/sqft. Therefore, with the area specified, the solar thermal power available for the given area on the roof is 396,000 Btu/hr which is not enough energy to meet the specified load. An area of approximately 8 acres would be required to meet the load. The roof also tends to be the area where large equipment gets placed such as air handling units, generators, egress pathways, and cooling towers. In this way, as acknowledged in the Mazzetti write up for Stanford Health Care, a number of acres are needed to satisfy the load requirements of a large hospital so the solar thermal collector application may limit the use cases to more rural areas.
Storage and control strategies need to be improved for hospital settings in the case of non-continuous supply of solar energy. Humidification needs in a hospital are important to control spread of infection and disease, so the system needs to be reliable and operable 24/7 which is still not certain with a solar thermal system.
Financial analysis and business case
Electric Steam Generators
From DriSteem, the operational cost is a major barrier to using electric steam humidifiers. An isothermal humidification system in Minneapolis with a 100 lbs/hr humidification design load humidifying 13,000 CFM with 30 percent outside air to meet desired conditions of 70F and 40 percent RH would produce approximately 265,000 lbs of humidification in one year. As of July 2020, commercial utility rates in MN are $0.087/kWh for electricity and $7.08/1,000 cu ft for natural gas. It would then cost $8,699 using an electric steam generator and $2,366 using a high efficiency gas-fired steam generator. In San Francisco, the natural gas rates are $8.50/1,000 cu ft and the electricity rates are $0.11/kWh. Taking a look at the expected tripling in cost of natural gas by 2030, the cost of the electric system is more comparable to that of the natural gas system. Especially when looking toward an 80 percent clean energy system by 2030, the cost of electricity generated by renewables will significantly decrease. There could also be policies put in place for fossil fuel-fired power plants to pay for the greenhouse gasses they emit.
Concentrating Solar Collectors
There are currently federal investment tax credits available for installation of solar thermal technology on new construction. Through the end of 2020, you can claim 26 percent and through the end of 2025, you can claim 22 percent for the investment tax credit.
The US. Department of Energy’s Solar Energy Technologies Office has set a goal to reduce the cost of concentrating solar power from $0.98/kWh in 2018 to $0.05/kWh by 2030. Concentrating solar power can deliver electric power for $0.10-0.20/kWh in 2021 with potential for under $0.10/kWh. These costs are higher than wholesale prices in the US, but they are lower than PV and could be attractive in the future if fossil fuel usage becomes constrained.
Solar collectors used in industrial and commercial processes, such as cleaning, drying, sterilization and pasteurization, heating of production halls, can reach energy savings of 75 percent to 80 percent with payback periods under five years, according to the Solar Heating & Cooling Program. Further development of high performance collectors will improve the cost effectiveness of higher temperature applications.
A discussion around Sterilization in Healthcare Systems
Below is an interview with Scott Czubkowski PE, CHC, National Director - Energy & Facility Performance for MedExcel Facilities Management conducted by Heather Burpee and Walt Vernon.
This interview discusses the challenges of sterilization in healthcare systems, specifically focusing on the inefficiencies of traditional steam systems and the potential for decarbonized sterilization. Scott Czubkowski highlights instances where design engineers specified unrealistic sterilization requirements, leading to unnecessary costs and upsizing. The use of electric boilers and natural gas backup boilers are proposed as a cost-effective solution for sterilization, emphasizing the importance of accurate data and actual system design. The discussion also explores challenges with cart washers and tray washers in non-traditional healthcare settings and proposes a thermal battery system as a solution. The participants discuss case studies of retrofitting healthcare systems to be more energy-efficient and the need for collaboration and accurate information in the industry. Lastly, water conservation techniques, the use of hybrid systems, and the potential for CO2 heat pump technology are mentioned. Overall, the video emphasizes the importance of optimizing sterilization processes in healthcare systems while considering various factors such as power limitations, water quality, workflow efficiency, and sustainability.
Case Study: Concentrated Solar Collectors
The Steinway & Sons manufacturing facility in New York City used a rooftop concentrating solar thermal system that produces temperatures from 320-350°F to power a double-effect absorption chiller and create low pressure steam. Maintaining humidity is important to control the moisture content of the wood components. In the summer, the hot water drives a double-effect absorption chiller to provide dehumidification and cooling. When dehumidification is not required, the collectors generating hot water above 275°F will circulate through a steam generator to produce 15 psig of steam to offset a portion of the 1200 kBtu/hr load. The low pressure steam system provides process and space heating and humidification.
The largest public hospital in Jordan, Al Bashir Hospital, uses a solar thermal collector connected to three heat exchangers to provide heat for the colorifiers of the hot water system, provide thermal energy for the hot water loop, and preheat the steam boilers.
Case Study: Electric Steam Generators - Sterilization
- Electric Steam Generators - Sterilization
- Do you know of an existing case study to highlight this technology? Please reply in the comments section, so that we might connect further!
Case Study: Electric Steam Generators - Humidification
Electric steam generation at the air handling unit and with in-duct humidifiers have been implemented for numerous projects in California. This decreases the need for steam piping to the location since the steam generator can sit next to the air handling unit or in the duct. These projects did result in an increase in the size of the emergency power generators which increased the electricity demand. The installation of these electric steam generators is helping achieve the goal of emitting net zero greenhouse gasses from its buildings and vehicles by 2025.
For Stanford Health Care, Mazzetti is analyzing alternative ways to generate steam for process loads (sterilizing and washing) and HVAC humidification that do not require fossil fuels. They looked at a number of options including unitary steam generation, steam generation per building, creating a new electric steam plant, and a solar thermal/solar electric power plant. The unitary steam generation option entails providing local steam generators for each piece of equipment. This option works if there is physical space and amperage capacity in the electrical equipment to add this load. The steam generation per building option requires five new steam generators to be added to the roof of the building which includes two redundant generators. Unitary steam generation requires additional utility service capacity since the existing infrastructure in the building cannot handle the load. The creation of a new electric steam plant adds three new steam generators along the existing steam line with one redundant generator. This option also requires the addition of more utility service capacity. The creation of a new solar thermal/solar electric power plant requires land to provide the 6,600 pounds per hour of steam: a solar electric plant that generates up to 3,300 kW needs 6 acres for the array and a 500 sq foot structure to house electrical gear while a solar thermal plant would need 4 acres for the array and a 500 sq foot structure as well. Given this study, there are many advantageous options to integrate steam into an existing system without needing to use fossil fuels.
According to DriSteem, Boston Scientific used electric humidification to reduce energy and maintenance costs. Electrode humidifiers were installed, but did not offer the ability to run constantly since this technology required frequent draining, filing, and reheating. Replacing the electrode humidifiers with resistive-element humidifiers from DriSteem reduced energy costs by 38 percent because of reduced need for heating make-up water. Maintenance costs were also reduced by 90 percent since electrode cylinders did not need to be replaced or refurbished.
Comments
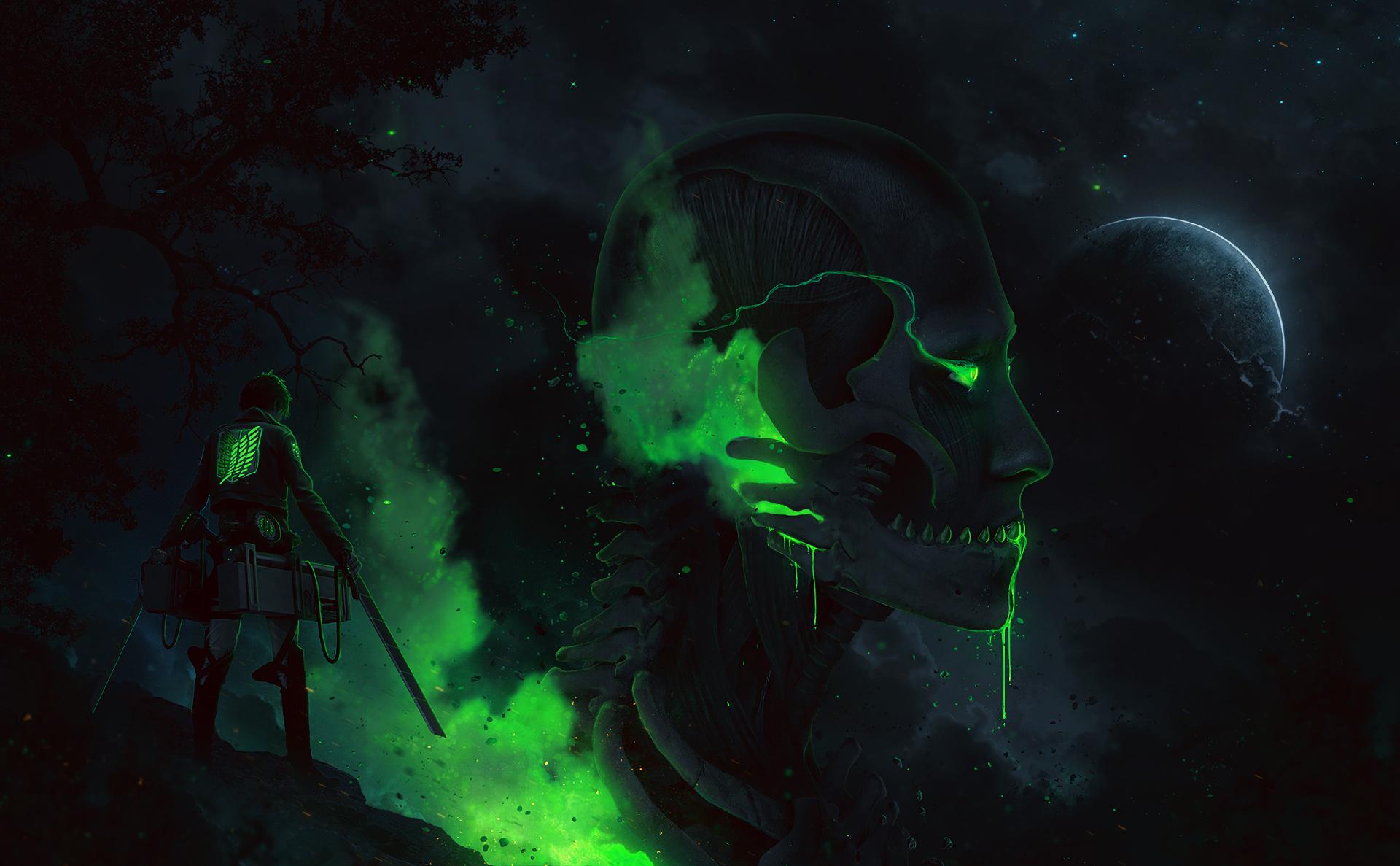
John Doe
8 seconds ago
Lorem ipsum dolor sit amet consectetur adipisicing elit. Quisquam, voluptatum. Lorem ipsum dolor sit amet consectetur adipisicing elit. Quisquam, voluptatum.
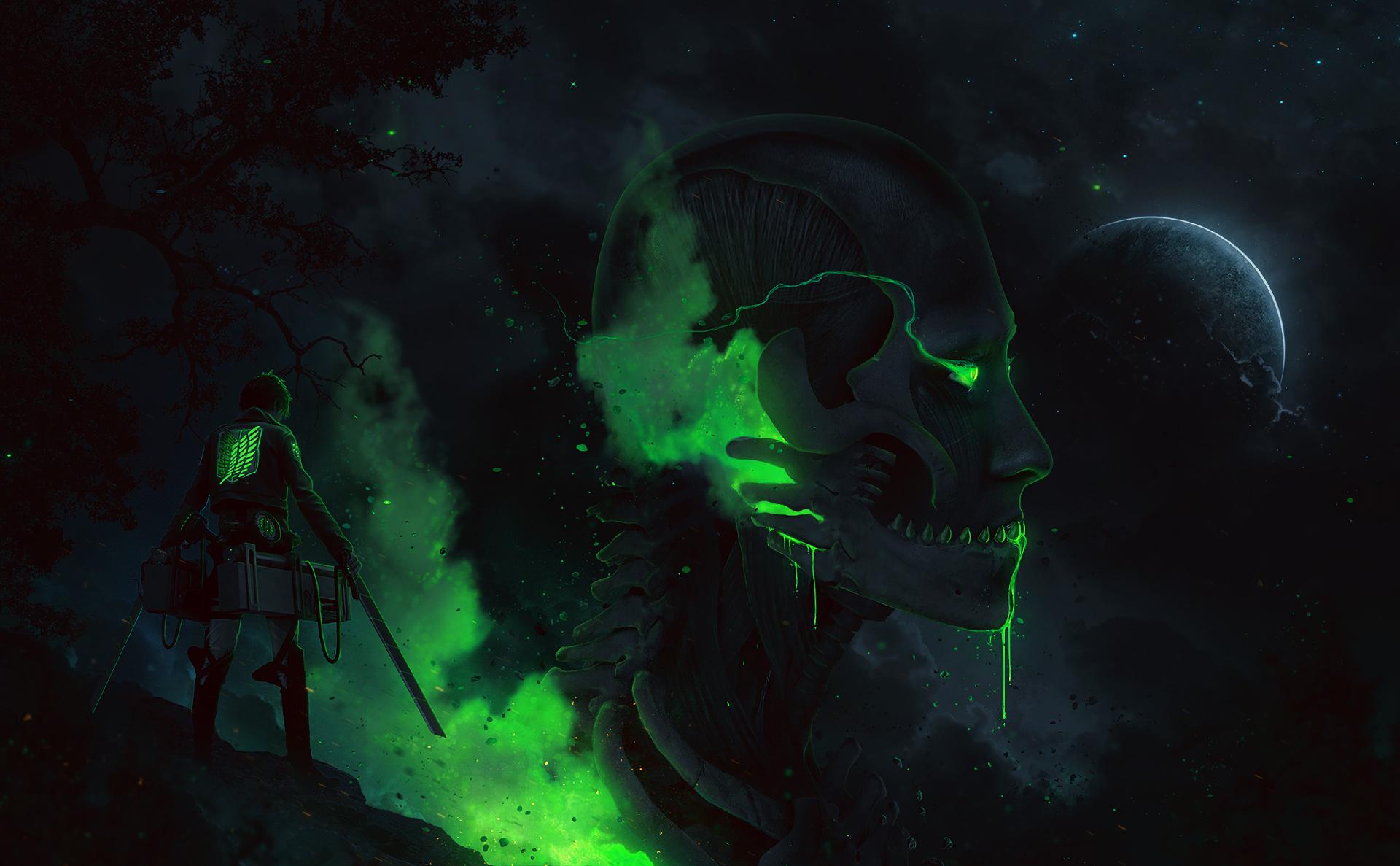
John Doe
18 seconds ago
Lorem ipsum dolor sit amet consectetur adipisicing elit. Quisquam, voluptatum. Lorem ipsum dolor sit amet consectetur adipisicing elit. Quisquam, voluptatum.