Welcome to the Decarb Guidebook
Approach
Benchmarking
Building Codes & Design Standards
State & Local Regulations
Technologies: Load Reduction
Technologies: Dehumidification
Technologies: If you must have a gas-fired boiler
Technologies: Central Plant
Technologies: Domestic Hot Water
Technologies: Steam
Technologies: Load Shifting and Energy Storage
Technologies: Emerging Technologies
Motivation Program
Pilot Projects
How to Pay for Decarbonization
Community Discussions
Workshops
Thermal Storage (HW and CW)
Resiliency and reliability are necessary for healthcare facilities. And backup energy storage ...
Executive Summary
Thermal energy storage (TES) systems take advantage of excess energy production, or energy made available during cleaner times of day, to create chilled or hot water in order to satisfy a building’s conditioning loads at a later time. This is also known as ‘load shifting’, in which a building’s conditioning loads are in essence shifted to a more effective time of day. “Effective” can mean less expensive to purchase from the utility or during a time when low carbon generation sources are available. Examples can include creating chilled or hot water during the daytime when solar energy is readily available, to use overnight. In general, power generation is less clean at night, on top of additional demand surcharges from power utilities. Implementing chilled water TES can cut utility demand by 20%. Depending on the cleanliness of the utility, this can translate to a 10% reduction in scope 2 carbon emissions. Implementing hot water TES seeks to shift heating loads to more effective times. If a facility utilizes natural gas boilers, heat rejection from heat recovery chillers can be captured during the day, and used for heating loads overnight. If electric boilers are used, the same methodology is applicable for chilled water TES, in which tempered water is produced during the day when clean energy is available. By decreasing usage of natural gas boilers, a facility can reduce its scope 1 emissions by 10-15% by implementing hot water TES.
Figure 1. Lipp thermal storage tank
Thermal Energy Storage
Technical Description
Background
Thermal energy storage (TES) in general works by using energy which was transferred to a storage medium at some earlier time. This can be in the form of a substance that is either warmer or colder than ambient conditions. Due to its convenience, this is typically in the form of chilled or warm water which can be used to satisfy a building’s cooling or heating demands. It is used in order to shift a building’s energy demand to a time that is either cheaper or cleaner to use energy.
An ideal thermal storage medium has a high thermal mass, or its ability to store thermal energy relative to its mass. This can be a combination of high mass density (a boulder), high specific heat (water), or a material with both (water again). A material with low thermal mass is air, which is why the ideal storage medium would have as little airspace as possible. This has led to the usage of rocks, sand, and water as popular materials for thermal storage. This is the foundation for ground source heat pumps as well, which are highlighted in chapter 3 of the guidebook. In a thermal storage context, a large sand bed which is cooled overnight by both mechanical and natural means, can surround chilled water piping, which provides cooling during the day. The sand bed would provide a medium to absorb large amounts of thermal energy, without changing temperature. Although sand and rocks are cheap and readily available, the heat still needs to be transferred to/from the water supply. Water is an excellent medium for thermal energy storage due to its high thermal capacity and availability.
TES systems can be utilized over a daily ‘diurnal’ or a seasonal time scale. Diurnal methods typically charge the tanks during the day or night, and discharge during the opposite time. CHW systems can be charged overnight when outdoor temperatures are cooler and electricity is cheaper to purchase. The water is then used during the day for the building’s cooling loads. HW systems can be charged during the day when excess renewable energy may be available, and utilized at night when building heating loads may peak. Seasonal storage takes advantage of plentiful renewable energy in the form of solar energy during the Spring and Summer, to constantly charge TES tanks. The water is stored until it is needed during peak months later in the year. CHW storage will be charged during the Fall and Winter, and utilized in the Spring and Summer. HW storage will be charged during the Spring and Summer, and utilized in the Fall and Winter. With seasonal storage systems, the water should still be accessible at all other times in case of extreme seasonal conditions, as has been occurring more often due to climate change. An example could be 75 degree day during a California winter.
In general, the power grid is also ‘greener’ during warmer months, when utility-scale solar photovoltaic and site-scale solar thermal energy is most available. The opposite is true in cooler months. For sites at higher latitudes, this is an excellent method for reducing natural gas usage for heating, in colder/darker months. Long term storage can still be charged whenever excess heat or cooling is made available, and used as frequently.
Hot Water TES
Hot water thermal energy storage is an economical means of storing heated water by reusing excess facility heating or from low carbon heat sources when available, which reduces the peak natural gas demand for the facility, reducing its overall carbon footprint. Heat can be extracted from waste heat from heat recovery chiller systems and combined heat and power systems, and generation from electric boilers can be used for heating demand at a later time. Low carbon-intensity heat sources include solar-thermal water heating, highlighted in Solar Thermal Water Heating. A facility that uses hot water thermal storage can expect to reduce its natural gas usage by 10-15%.
Facility heating demand is present consistently throughout the day, whether it is creating domestic hot water for showering and handwashing during the day, or space heating at night. Excess electricity produced by renewable energy sources such as wind and solar which peak during the day, can be used to operate electric boilers creating hot water at suitable temperatures. This water can then be stored in a Thermal Energy Storage (TES) tank, and discharged as needed. This can eliminate the need to use natural gas boilers, eliminating their carbon emissions. With a TES tank, the water is already tempered and can be used immediately. The first step to reducing energy waste in any system is minimizing the number of energy transfers.
Chilled Water TES
Chilled water TES has the most flexibility for The chilled water cooled at night, is used during the daytime for a building’s cooling needs. Chilled water energy storage is covered in a separate chapter.
Design considerations
Space heating alone accounts for around 36% of energy use in commercial buildings, and 35% in healthcare buildings. This includes all space heating, air preheating, and domestic hot water demands. Hydronic systems are the most common means of space heating in buildings. Typically, a design temperature of 120-140°F is used to heat air to approximately 85°F before entering the zone.
In colder climates, total building heating demand will peak at night due to envelope heat loss. However, in healthcare applications the greatest heating demand will likely come from supply air reheat due to high ventilation requirements. Air tempering is crucial for maintaining thermal comfort, especially in patient rooms. This makes air reheat a major driver of heating demand, during any time of day.
Hot Water TES systems can be charged directly and indirectly, increasing their project flexibility.
Directly: It is likely that a facility concerned with decreasing or eliminating its scope 1 emissions from natural gas usage will implement electric boilers. During low heating demand times, these boilers can be used to create hot water to be sent to the TES. Implementing electricity emissions optimizations also allows the usage of boilers, powered by the local utility, during the cleanest times of day. This is typically when renewable energy is plentiful during the day, which fortunately will coincide with lower heating demand. This effectively charges the TES by using the cleanest possible energy source. During ‘dirtier’ times of day for energy production (such as at night, or other high electric demand times), the TES will be used for heating, saving on scope 1 emissions from the grid.
Indirectly: Combined heat and power (CHP) systems are common for large campus healthcare facilities. Waste heat as well as steam from these operations can be utilized to create hot water for TES. Additionally, during low electric demand times, electricity generated by CHP can also be used to operate electric boilers to charge the TES directly. In this way, the CHP plant is able to operate at a more consistent pace. It will no longer be required to ramp down during low-demand times, and can operate at its best efficiency point more often.
Generally, a stratified storage tank strategy is utilized for both CHW and HW systems. Density differences due to the difference in supply and return temperature lead to a natural separation of fluid sections, marked as the ‘thermocline’. The thermocline can only be a few inches thick, with a 20 degree temperature difference between the top and bottom as shown in the figure below. More efficient TES systems are marked by a relatively thin thermocline (relative to the tanks height/volume) Warmer water remains near the top, cooler water remains near the bottom. For heating systems, supply water is pulled from the top of the storage tank, and the return is routed near the bottom. For chilled systems, supply is pulled near the bottom. Maintaining a defined separation between supply and return sections is important to maintaining a consistent supply temperature. This requires the prevention or minimization of mixing which can occur when return water is reintroduced into the tank. To minimize this, return water outlets use diffusers, which allow the water to flow at low velocities, preventing turbulence which can cause mixing.
Figure 2. Stratified tank diagram
Hot water systems serve hydronic heating applications by pulling water from the top, and is returned at the bottom. These systems, when paired with solar thermal installations, create an additional means of generating carbon-free hot water during the day for storage.
A facility cannot combine CHW and HW storage into the same tank due to large differences in usable supply temperatures for these systems. Usable temperatures for hot water systems can range from 100-140F, where chilled systems require a supply temperature from 40-50F. Increasing the temperature difference within a tank increases the thickness of the thermocline, decreasing the usable range for the tank. Financial analysis paired with annual energy modeling should determine whether it is appropriate to use one temperature range over another, or whether having dual tanks is feasible.
For HW systems, storage tanks should be sized in order to facilitate the ‘right-sizing’ of boilers. This topic is explained in greater detail in ‘Chapter 2 - Boiler Right Sizing’ of the Decarb Guidebook. That is, allowing heat generation equipment to be sized for the most common load case, instead of peak demand. The TES should be sized, at minimum, to cover the difference between expected peak, and the capacity of the heating plant. Additional capacity will further decrease the energy consumption of the heating plant, however it will come at additional cost. The energy capacity is proportional to both the tank volume and the desired temperature difference. To decrease pumping costs, large temperature differences (typically 40F) are recommended.
Figure 3. Sizing strategies using cooling loads
There are a few sizing strategies for determining TES capacity. The capacity is proportional to the tank volume, and desired temperature ranges. Typical storage supply temperatures can range from 39 to 42°F, and return temperatures can range from 55 to 60°F. This wide range is application dependent, however a 20 degree temperature differential is often applied. Typically, the TES system should be sized at a minimum to supply enough cooling capacity to meet peak demand, when the chiller plant is sized for average load. If allowable, the TES can be oversized in two ways. The first allows the chiller to be sized below the peak cooling load. Engineering best practices should be used when determining a deliberate undersizing of the chiller, as it still needs to be able to fully charge the TES over a reasonable amount of time. The next situation evaluated observes the impacts of large undersizing of the chiller, and subsequent large sizing of the TES. This may be appropriate for non-mission critical facilities, and facilities with very predictable cooling loads. This also assumes that the CHW TES system can be charged fully before the next thermal cycle. This also requires a large storage system, which may not be feasible due to financial or spatial constraints on site. The best practice would then be to oversize the TES as desired, and ‘right-size’ the chiller, where the chiller is sized for average loading. In this example, is 60% of peak demand over the year. This allows for additional cooling capacity in the case of extreme heat events, or multiple simultaneous cooling demands, such as building cooling in parallel with CHP inlet cooling.
CFD analysis has shown that storage tanks with an aspect ratio of 1 (tank Height relative to its diameter) have the lowest degree of heat loss. However, due to space constraints, it may be advantageous to have a tank that is taller than it is wide. As aspect ratio approaches a value of 3, thermal stratification increases. This creates a taller temperature gradient in the tank, and increases the chance of a decrease in supply temperature. So, in order to maintain a consistent supply temperature, a low aspect ratio should be prioritized. For a facility requiring 940 gallons/minute of heating hot water during its peak hour, this would require a tank with a height of 22’-6” and a diameter of 20’-6” if the aspect ratio is 1.1, or a height of 25’-4” and diameter of 19’-6” if the aspect ratio is 1.3.
Retrofit and New Construction
Although TES is suitable for new construction and building retrofits, integrating it holistically into a building’s hot water loop is easier for new projects. This is the easiest time to find space on site for storage tanks. It is also the best time to connect into the hot water loop. For an existing facility, equipment shutdowns would be required to add additional connections. For new construction, TES will help decrease equipment upfront costs by allowing usage of less-oversized boilers. In retrofits, using TES could allow for additional building demand capacity, while keeping existing heating equipment.
Control strategies
If space permits, staging TES tanks in parallel allows for greater supply temperature consistency. As a TES is discharged, the location of the thermocline approaches the water outlet, causing a change in supply temperature. When this is detected, the
TES is best used for loads which are cyclical or otherwise predictable. A charging cycle can be performed in advance, if facilities anticipate high conditioning demand loads, such as forecasted abnormally hot or cold weather, leading to abnormally high cooling or heating loads for the time of year.
How does this decarbonize?
This shifts building load to lower peak times, decreasing the cost of energy. For example, the utility SMUD offers a cost savings of 38% during winter and summer months. This also reduces the negative effects of intermittent renewable energy. Chillers and boilers will have improved part load efficiency and can be sized closer to their expected demand, as the TES will smooth demand peaks, allowing it to operate at a consistent level.
Implementation
Barriers: Cost
TES requires large storage tanks for consistent hot water temperature, leading to substantial upfront costs for the tank(s) and additional piping
Barriers: Technical
The boilers are more likely to be constantly running, since they must recharge tanks during off demand hours. Mixing in stratified tanks increases the chilled water supply temperature, decreasing its effectiveness for building cooling.
Strategy
TES is especially suited for cooling loads which are cyclical and predictable from weather patterns or facility programming. With properly sized chillers for actual building demand, the chillers can operate at their most efficient operating point. This is due to the TES smoothing peak loads, allowing the chillers to operate at a more consistent level. Using low velocity flow diffusers can prevent mixing within the stratified tank. When used in tandem with solar PV installations, this allows a non-carbon based method of energy storage for both chilled and hot water.
Financial analysis and business case
Determine the simple payback period for the cost of additional storage and equipment, with the cost savings that comes from creating hot water during low demand times. The ability to make hot water during the day from clean sources reduces facility carbon emissions and can reduce utility usage overnight.
Simple payback period can be determined by comparing capital costs of energy storage, with capital savings from chiller downsizing and operational savings during peak times. From the DOE, capital costs for TES can be between $100-$200/Ton-hr. For a 20 degree temperature differential, this results in $1.39-$2.79/gallon of storage. [3]
Analyze the cost savings from being able to use alternate energy sources throughout the day. Typically, a peak cooling load of 100 tons is necessary to achieve economic feasibility [2]. Additionally, Chilled water TES also serves as a water source for fire fighting which can decrease infrastructure damage during fire events.
Case Study: Veterans Administration Medical Centers
Case study featured in Engineered Systems magazine.
Dallas VA Medical Center
The thermal energy storage system is helping the Dallas VA Medical Center shift a significant portion of its hospital's energy demand away from the peak-cost period to a lower-cost period.
The hospital relies on a stratified water thermal energy storage system with 3.3 million gallon capacity.
The storage tank is filled with chilled water every night. Then every day, from noon until 8 p.m., the hospital draws its chilled water from the tank to meet its cooling load, instead of requiring continuous electric service to operate on-site chillers. As an added feature, the thermal storage system doubles the capacity of the hospital's central plant. If the hospital expands, the VA could use the thermal storage system and its existing cooling system at the same time, avoiding additional capital investment.
West Haven (CT) Campus of the Veterans Affairs Connecticut Health System
The hybrid central cooling plant has 6000 tons of thermal storage that ties in with their a steam absorber, electrical centrifugal chiller, and primary/secondary pumping.
The second phase of the project expanded the plant capacity with a 6,600-ton/hr ice thermal storage system. During peak demand times for cooling, ice is utilized to lower the discharge chilled water temperature from 44 degrees F to 40 degrees. With the lower chilled water temperature, the need for increasing the chilled water distribution system was not required, providing a first-cost savings of $280,000.
The ice thermal storage system saved $650,000 in first cost and is saving approximately $100,000 annually in operating costs. There are other intangibles that factor into the savings as well. As Palazzi points out, the VA is saving a lot of money in maintenance costs by utilizing the existing chiller plant and its primary pumping system and auxiliary equipment, eliminating the need to have additional equipment installed.
Comments
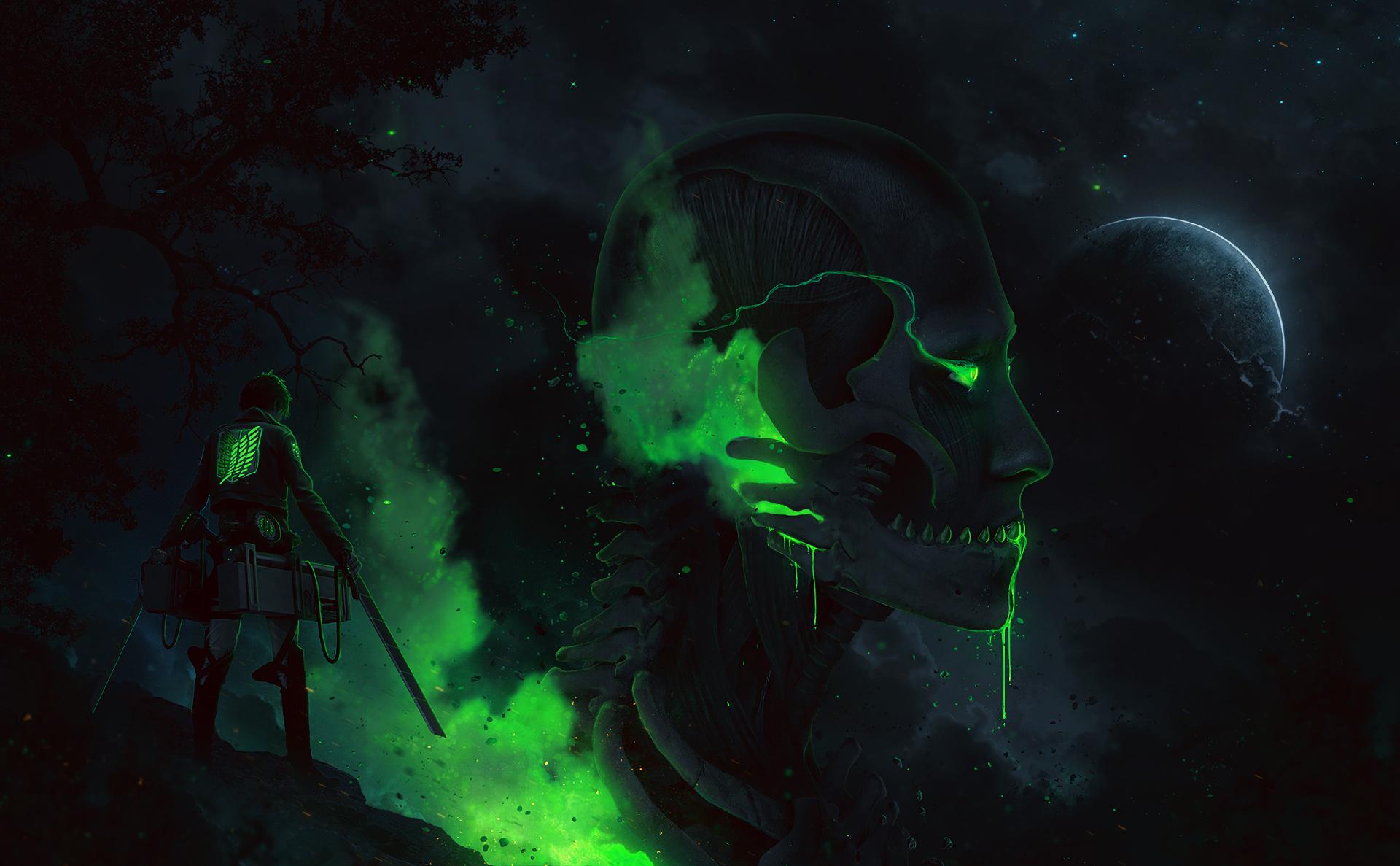
John Doe
8 seconds ago
Lorem ipsum dolor sit amet consectetur adipisicing elit. Quisquam, voluptatum. Lorem ipsum dolor sit amet consectetur adipisicing elit. Quisquam, voluptatum.
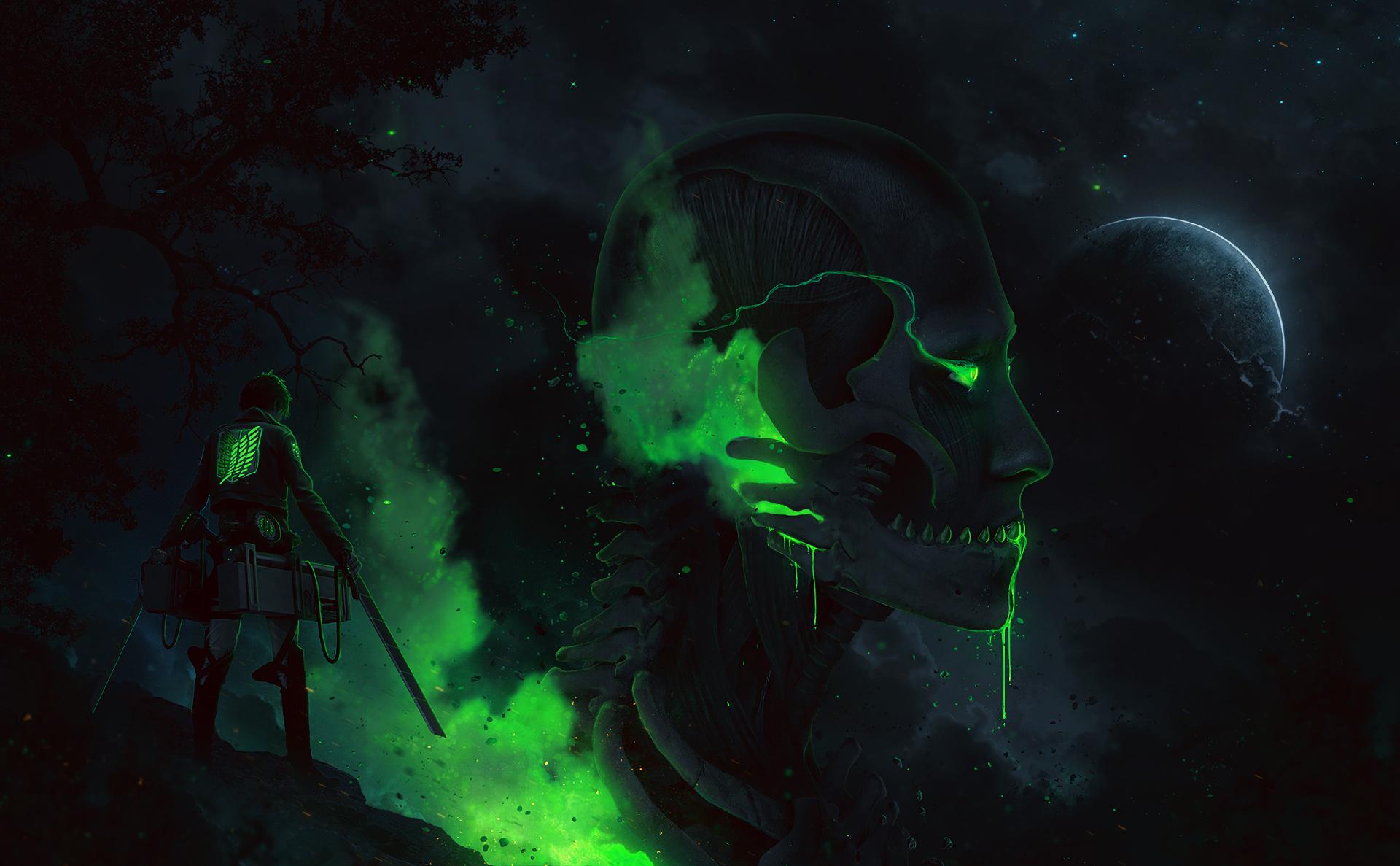
John Doe
18 seconds ago
Lorem ipsum dolor sit amet consectetur adipisicing elit. Quisquam, voluptatum. Lorem ipsum dolor sit amet consectetur adipisicing elit. Quisquam, voluptatum.