Welcome to the Decarb Guidebook
Approach
Benchmarking
Building Codes & Design Standards
State & Local Regulations
Technologies: Load Reduction
Technologies: Dehumidification
Technologies: If you must have a gas-fired boiler
Technologies: Central Plant
Technologies: Domestic Hot Water
Technologies: Steam
Technologies: Load Shifting and Energy Storage
Technologies: Emerging Technologies
Motivation Program
Pilot Projects
How to Pay for Decarbonization
Community Discussions
Workshops
Executive Summary
Over 20% of the gas consumed in a hospital is wasted through the boiler flue. Gas-fired boilers are used in hospitals for both hydronic and steam systems providing heating hot water, domestic hot water, humidification, and sterilization. The thermal efficiencies of traditional boilers are 80% or lower. Stack gas economizers utilize the heat of the stack flue gas that would otherwise be exhausted out of the system, resulting in efficiency gains proportional to the amount of energy recovered. In hot water boilers, low-temperature return water that will condense flue gas can achieve up to 95% thermal efficiency. In steam boilers with warmer return water temperatures, achieving higher efficiency gains requires a cooler heat sink such as boiler water make-up or hot water preheat.
While this technology can improve the efficiency of the boiler plant and reduce natural gas consumption of a facility, it is fairly limited in its overall impact on carbon emissions in that it still relies on the combustion of natural gas to produce heat. This should be considered an interim step in the overall decarbonization process.
Boiler stack gas economizers are worth considering for facilities that want to reduce energy costs, improve performance of the boiler plant, and reduce Scope 1 carbon emissions from natural gas consumption while utilizing the remaining life of their boilers. Typically, the payback on a condensing stack gas economizer occurs after 1-4 years.
Stack Gas Economizers
Technical Description
Background / How it works
In a traditional hot water boiler, natural gas is piped to a heating chamber and ignited. The burned gas provides byproducts which are chemical elements, such as carbon dioxide, hydrogen, and oxygen, as well as heat. This heat is transferred to water pipes inside the boiler through an internal heat exchanger, which is then pumped to heating coils in air terminal boxes, fan coil units, and air handling preheat coils throughout the facility. The superheated byproducts are exhausted from the boiler through the flue out of the building. In traditional boilers, this heat energy is exhausted to the atmosphere and considered waste heat.
A traditional hot water boiler can be retrofitted with a condensing economizer to in essence create a condensing boiler exhibiting similar efficiency gains 10-15%. (refer to Condensing boilers). When water vapor condenses in this system, dissolved NOx particles make the condensed liquid acidic and corrosive. Due to this, further considerations such as heat exchanger material and a neutralization unit, in addition to drainage, are necessary. Figure 1 below is a system diagram showing how an economizer is installed to an existing boiler system.
Figure 1. Economizer piping and valve apparatus
In a steam boiler, the feed water to the boiler is not sufficiently cool enough to condense the flue gas during normal operation. However, if the boiler cycles often, some flue gas will condense and nitric acid will wear a non-stainless steel flue gas stack.
With the installation of a stack gas economizer on a steam boiler, the same considerations of a condensing economizer will be necessary but with, at most, half the efficiency gains.
If a cooler heatsink is available, many manufacturers do offer two-stage economizers where the first stage preheats the steam boiler feedwater and the second stage provides heat to the boiler feed water or make-up water.
Design considerations
The threat of corrosive liquid in the flue gas stack and heat exchanger necessitates a high-grade stainless steel be used in the heat exchanger flue and flue gas stack. A Stainless steel condensate drain piping to a neutralizing basin (filled with limestone as a common neutralizer) is needed before discharging into the building drainage system,
In order to ensure water circulation through the economizer at all times, a bypass line should be used for returns to the deaerator tank. A recirculation flow keeps the water from boiling in the economizer when the steam generator isn’t calling for feedwater.
Additional controls should be installed to monitor the temperature of the flue gas into and out of the economizer as well as the recirculation flow.
The efficiency benefits of a condensing economizer are best realized with low temperature boiler feed water. Refer to Best Practices and Control Strategies within Condensing boilers.
Advantages
Energy efficiency: Recovering waste heat from the boiler flue improves the efficiency of the boiler by preheating the feed water. This process reduces the amount of natural gas consumed by the boiler to meet the heating load.
Reduced NOx emissions: Lowering the flue gas temperature with an economizer aids flue gas recirculation strategies for meeting NOx standards.
How does this decarbonize?
Adding a stack gas economizer to an existing boiler system will improve the overall efficiency by 10-15% by recovering waste heat. When waste heat is recovered from the boiler flue, it reduces the amount of natural gas that is consumed by the boilers to meet the same heating output. Less natural gas burned means less Scope 1 stationary combustion emissions.
However, this technology is fairly limited in its overall impact on carbon emissions in that it still relies on the combustion of natural gas to produce heat. This should be considered an interim step in the overall decarbonization process.
Implementation
Barriers: Culture
Many practicing engineers do not design condensing systems well. Engineers are familiar with this technology, only as represented by manufacturer literature.
Barriers: Technology
In the case of a retrofit in a system designed to condense flue gas, replacing the flue gas stack with one of corrosive resistant material is necessary for the longevity of the boiler. There may be difficulties with this replacement if the flue gas stack leads to a shaft, as opposed to leaving the building directly.
Strategy
To implement this technology with a hot water boiler, it is recommended to evaluate the existing heating hot water requirement, with an emphasis on the actual low-load needs.
- Assess whether the reduction in supply water temperature has any impact on the overall comfort of the building.
- This can be achieved by adjusting supply water temperature incrementally over time, and documenting indoor conditions.
- If the building can function with the supply water temperature at 130℉, this building could achieve the higher end efficiency gains associated with a condensing (economizer fitted) boiler.
To implement this technology with a steam boiler, it is recommended to evaluate the energy available within the flue gas for transfer and perform a cost analysis.
Financial analysis and business case
Referencing Cain Industries’ boiler economizer white paper, the average equipment payback on a 100-800 HP boiler is 1 to 2 years. On average, thermal efficiency increases 4 - 10%. The following cost analysis assessing a Mazzetti installed system is in line with the anticipated equipment payback reported by Cain Industries.
Table 1: Cost estimate for installing a single economizer unit including the stack and condensate run-off
The labor cost was estimated at 30% of the capital cost for the economizer. An inflation calculator was used to estimate the current day cost of a stainless steel economizer.
Table 2: Natural gas savings estimate using plant performance data
The energy needed and thus the natural gas consumption (as reported within the table) was calculated using the following equation.
The difference in natural gas consumption with the 2021 average commercial utility cost of natural gas in CA ($0.96 / therm) was used to estimate the yearly natural gas savings of this project.
Table 3: Project payback
------------------------------------------------------
Citations
- DeFrees, J.; Stuckey, R.; (Nov, 2007). Condensing Economizers. Ashrae Journal, 16-23. This example is of a condensing unit within a small dairy processing facility. The payback was within 4 years.
- http://www.cainind.com/case-studies-exhaust-heat-recovery.php This example is a non condensing unit within a 75-bed acute care hospital. Payback was within 2 years
- https://natural-resources.canada.ca/maps-tools-and-publications/publications/energy-publications/heat-recovery-boiler-stack-economizers/5931 This example is a condensing unit in a non-healthcare facility. The payback was within 4 years.
Case study: Oconomowoc Hospital
- ProHealth Oconomowoc Memorial Hospital, Oconomowoc, WI,
- A 75-bed, general acute-care hospital with a paired 300 HP steam boiler. Three condensing stack gas economizers were fitted together recovering 408,000 BTU/h from the system operating at 1320 gpm. With the economizers, the boiler feed water increased in temperature from 227℉ to to 266℉. The annual fuel savings was reported at $14,231 and the project annual ROI at 74%.
Case Study: Stanford Hospital Steam Plant
- Stanford Hospital Replacement Steam Plant, Palo Alto, CA
- The steam plant was designed as a Thermal Fluid system with 5 steam generators, each sized for 10,000 lb of steam per hour. A great opportunity for a stack-gas economizer; the thermal fluid heaters had a thermal efficiency of 78% with a stack gas temperature of 575℉. With the stack-gas economizer the thermal efficiency increased to 88.2%; Return water temperatures increased from 227℉ to 278℉. The economizer, although the system was not based on condensing temperatures, condensed flue gas which drained through stainless steel piping toward a neutralizing was accounted for by stainless steel condensate drain piping from the outlet of each economizer.
Internal Mazzetti Document
Comments
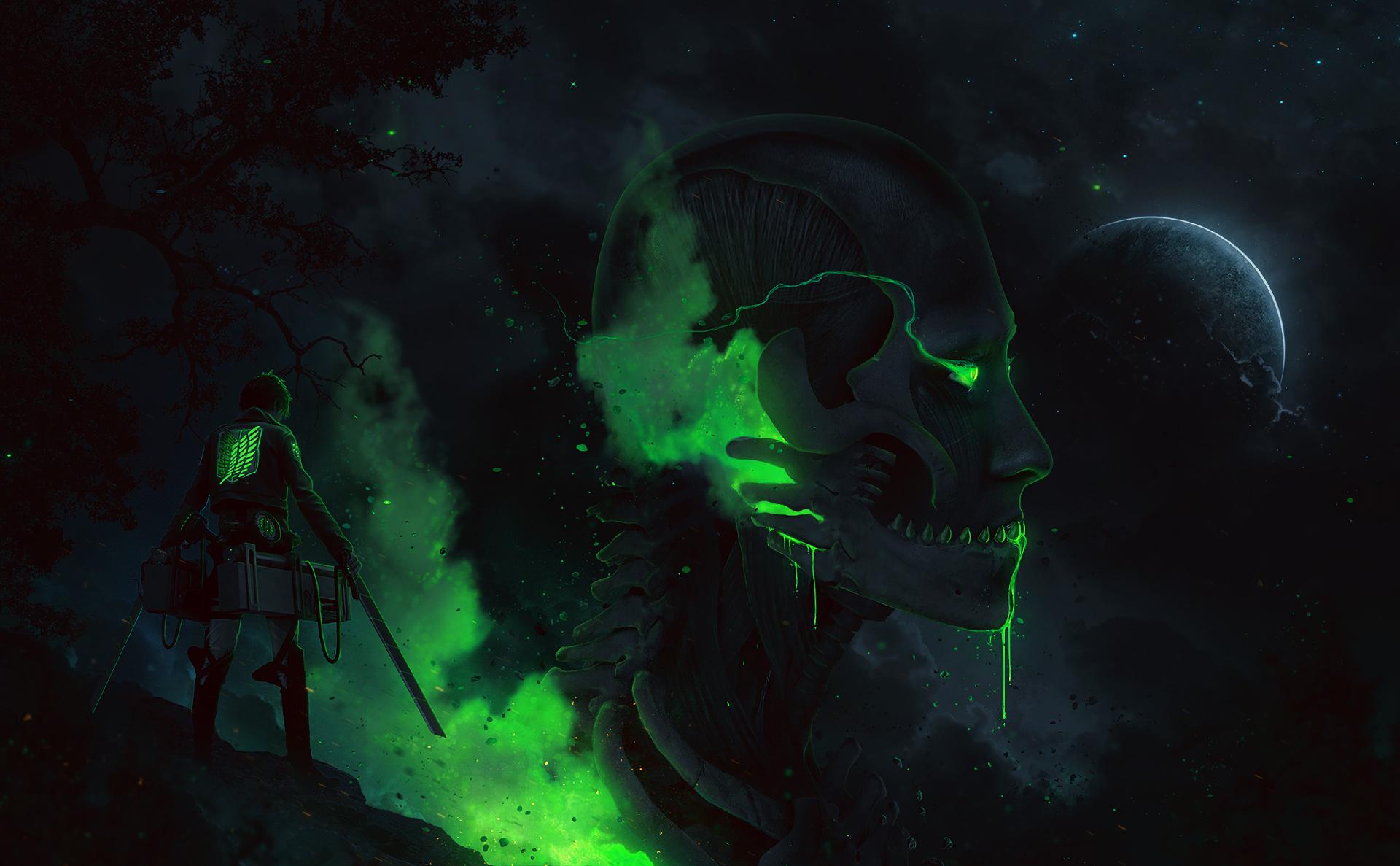
John Doe
8 seconds ago
Lorem ipsum dolor sit amet consectetur adipisicing elit. Quisquam, voluptatum. Lorem ipsum dolor sit amet consectetur adipisicing elit. Quisquam, voluptatum.
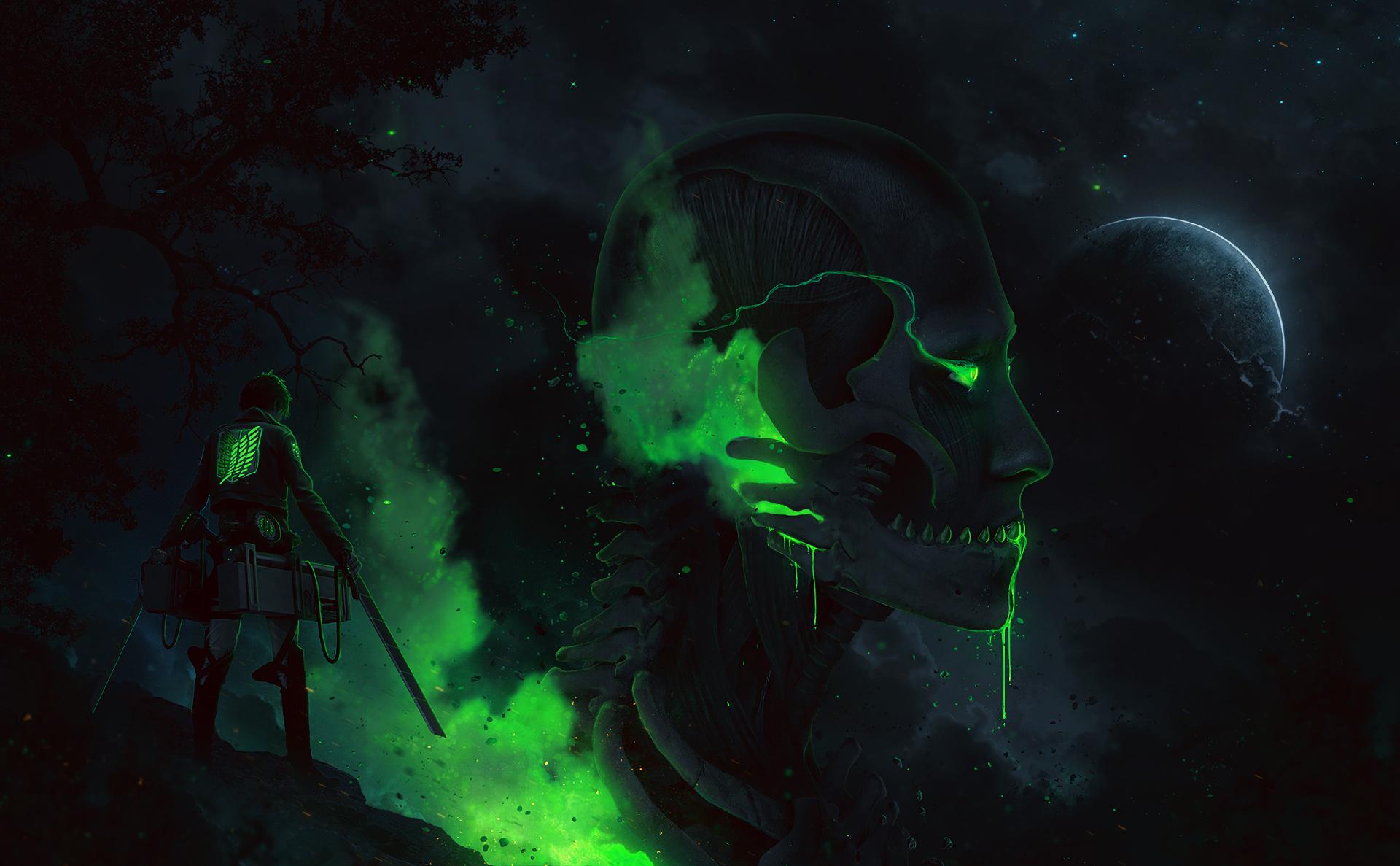
John Doe
18 seconds ago
Lorem ipsum dolor sit amet consectetur adipisicing elit. Quisquam, voluptatum. Lorem ipsum dolor sit amet consectetur adipisicing elit. Quisquam, voluptatum.