Welcome to the Decarb Guidebook
Approach
Benchmarking
Building Codes & Design Standards
State & Local Regulations
Technologies: Load Reduction
Technologies: Dehumidification
Technologies: If you must have a gas-fired boiler
Technologies: Central Plant
Technologies: Domestic Hot Water
Technologies: Steam
Technologies: Load Shifting and Energy Storage
Technologies: Emerging Technologies
Motivation Program
Pilot Projects
How to Pay for Decarbonization
Community Discussions
Workshops
Executive Summary
Executive Summary
Traditionally, hospitals burn natural gas to create heating hot water and steam for the facility. At the same time, the chiller plant works to remove heat from the building and reject it to the atmosphere. This requires electricity to both add and remove heat from the building.
A more efficient, and less carbon intensive approach to the entire heating system would be to use a heat pump system with heat recovery chillers, which run solely on electricity, requires zero on-site combustion, and recovers waste heat from inside the building to be repurposed for other heating needs such as space or water heating.
Heat Recovery Chillers and Heat Pumps
Central plant background
Traditional boilers vs heat pump heating
- Boilers in traditional systems use either combustion or electricity to create hot water. This leads to greater on-site carbon emissions and additional chiller load since that heat eventually must be removed by conditioned air. Heat pump systems circulate refrigerant throughout the building, which absorbs heat from the environment, and carries it to a central location to be repurposed or rejected.
Traditional chillers vs heat recovery chillers
- Chillers in traditional systems use electricity to drive a vapor-compression refrigeration cycle, which absorbs heat from returned chilled water, and eventually discharges it to the atmosphere in the form of heated air.
- Heat recovery chillers use the heat removed from chilled return water to create hot water for the building. Traditional chiller systems simply reject his heat to the atmosphere. Heat recovery chillers use the building chilled water system as a source of heat, rather than a waste product.
- The difference between heat pumps and heat recovery chillers is a matter of semantics. The two essentially work in opposite directions. A heat recovery chiller runs in order to make chilled water, that creates warm water as a result. A heat pump, is a machine that runs to make hot water, that also incidentally creates cool or chilled water.
The Issue at Hand
Hospitals are exothermic. That is, they produce more heat than they need. We run cooling towers or economizer cycles most of the year to remove that heat. Why then do hospitals also run boilers every day, year-round? During an air-cooled heat rejection cycle, air is discharged at a temperature below 120F. Thermal energy at this low of a temperature is known as ‘low-grade heat’, meaning it has little capacity to create useful heat, such as hot water at 140F. A process is required which would capture this energy into a more concentrated form, improving its usefulness.
Why is heating the largest end-use of energy in hospitals from North Dakota to Southern California? There are several reasons why this simultaneous heating and cooling is common, but to a large degree it comes down to temperature. The heat we’re rejecting exists at a temperature that is too low to be useful – so we use boilers to make hot water or steam at a temperature we can use to heat the building, make hot water, sterilize surgical instruments. What if there was a way to make all that low-grade heat useful? Would there be enough heat that we could stop burning fossil fuels?
FAQs
Q: Can heat pumps make water hot enough to heat the building?
A: Yes, but only if the system is designed to operate at 140F or lower. Easy to do in new construction. Older building hot water systems may have been designed for 160, 180, or even 200 degF hot water supply. Even so, we find that most hospital heating systems are over-designed and may operate at 140 with little or no modification. If you have an existing building, it’s an easy thing to check. Just start lowering your hot water temperature and watch what happens - if every space is satisfied when you get down to 140, you can probably use heat pumps.
Q: In our hospital, we shut down the chiller plant when the outdoor temperature is below 50. We get free cooling from the outside air. How can I use heat recovery?
A: First, let’s think about what “free cooling” means. If the outdoor temperature is 50F, you’re using that cool air to absorb heat from inside the building. That sounds better than running a chiller. But, what happens to that heat that is being absorbed? Exhaust fans remove that warm air and discharge it to the great outdoors. You’re throwing heat away? If you have heat pumps, you can extract that heat through cooling coils in the air unit or heat recovery coils in the exhaust. Why run boilers to make “new” heat, then throw it out the window?
Q: Has this been tried in hospitals before?
A: Absolutely! We have numerous case studies of heat recovery chillers being used to reduce the load on boilers. We have two projects, both located in Georgia, where heat pumps provide all space and hot water heating - there is no fossil fuel combustion on-site for heating. In both Georgia hospitals, pipe loops in boreholes store heat deep underground to carry the building through cold weather - below 25 degF. Those hospitals have been in operation since 2014 and 2015.
Technical Description
Design considerations
Heat pumps can be used to provide all space heating and domestic hot water production for hospitals, effectively eliminating on-site combustion of natural gas for these two large uses. During heating days, heat pumps are effective until temperatures dip below 25F. Although the systems can still operate, the compressor will work harder as condenser pressure requirements rise. This makes heat pumps most effective for ASHRAE Climate Zones 1-4. In zones 5-7 (Alaska), typical winter temperatures are often below 25F, and are much more extreme.
Heat recovery chillers can be applied in any cooling system in a hospital and can typically supply all heating needs in warm weather, but may not be able to provide all of the heating in the coldest weather. In some existing installations, heat recovery systems can satisfy all heating requirements when outdoor temperatures are above 25 degF. Below that temperature, a supplemental heat source is needed. Supplemental sources could include:
- A ground-loop heat exchanger, which uses the earth for thermal storage
- Data center cooling systems, kitchen refrigeration systems, or other year-round cooling equipment, which discharge heat into a heat pump system.
- Sanitary waste systems, via a specialized heat exchanger
- Waste-to-energy conversion systems (covered elsewhere in the Guidebook)
- Solar thermal heat sources, paired with thermal energy storage
In some parts of the country, it is common to use economizer systems - airside or waterside. These systems use very little energy for cooling, but operate under the principle of using maximum amount of outside air for free cooling. This is often done by modulating the proportion of outside air up to 100%, and discharging the remaining proportion of relief air. Reducing the use of economizers can extend the range of heat recovery chillers as the primary heat source for the building.
Typical gas-fired boilers have a combustion efficiency of 80-90%. Overall system efficiency of a steam boiler system is typically closer to 75%. Heat pump systems are more commonly rated in terms of Coefficient of Performance,or the ratio of output over input. A boiler system with an efficiency of 80% would have a COP of 0.8. This means the resulting heating energy from the combustion process is less than what you put into it, due to efficiency losses. With a heat pump system, the COP can be in the 2.5-7 range since the electrical energy being put into the system is used to move heat, rather than make heat.
Control strategies
Heat recovery systems in general are effective until the temperature difference across the building envelope is 25 degF. Heat pumps/heat recovery chillers should be used preferentially until this point, and supplemental heating via traditional boilers or GSHPs will provide the additional load.
Best practices
Diagram / map
Design Considerations
When to use a heat pump vs heat recovery chiller?
Existing buildings vs new construction
Generally, it is easier and more cost effective to implement an all heat pump system in new construction than in retrofit, but the principles apply to both. In warmer climates, where temperatures rarely dip into the 20s, supplemental heat may not be needed at all.
- Heating needs vs cooling needs
- Heating efficiency vs cooling efficiency
- Location?
- The cost effectiveness of a heat recovery chiller and heat pump combination system is dependant on it’s location relative to the ASHRAE climate zones.
- Geothermal Ground Source Heat Pumps (GSHP) work in a similar way to heat pumps. By absorbing heat from naturally warm ground water, hot water can be made combustion-free. This method also has 0% heat-loss from the generating body (in the form of heat rejection from a generation device into the facility). GSHPs are discussed in greater detail in the section in Ch.2.
How does this decarbonize?
Heat pumps run on electricity and do not use any natural gas. Using heat pumps as the only source of heat and domestic hot water can eliminate the cost of combustion equipment and the cost of the space they require, effectively using a slightly larger footprint for a cooling plant to provide both heating and cooling and eliminating the space required for a heating plant.
Implementation
Barriers: Codes
Regulations require onsite fuel storage for building heating. When heat pumps are used for that purpose, backup electrical power systems and their fuel storage fulfill the requirement without separate fuel storage.
Barriers: Technical
At time of this writing, mechanical equipment to provide heat recovery and heat pump heating is not uniformly reliable. A popular approach is a modular system that uses scroll compressors in various configurations to provide cooling, heating, or simultaneous cooling and heating, in a combination to match all of the loads. Because of the high and constant lift of heat recovery systems, capacity modulation of these systems is very limited. There are widespread reports of difficulty controlling these systems to match loads, leading to frequent compressor cycling, compressor failures, and failure to maintain system temperatures within prescribed tolerances. Other systems utilizing screw compressors may be more reliable, but equipment must be capable of modulating to match a wide range of load. Manufacturers are developing new equipment with intent to improve load matching and reliability.
Another barrier is the tools available to design engineers. Traditionally, design of heating and cooling systems has been focused on meeting the maximum load for each system, with provisions for modulating capacity for part-load operation. Design software has not been focused on the simultaneous heating and cooling loads. Energy modeling software can help to fill the gap, but is not intended as a tool for designing systems and selecting equipment. Thermal energy storage adds even more complexity. New tools are needed to improve designer confidence and reduce risk.
Barriers: Culture
Strategy
Experience shows that we can recover enough heat from the building to overcome losses from the envelope and outside air ventilation until the outdoor temperature goes below about 25 degF. Below this point, supplemental heating will be required to satisfy building loads, see the section on alternative sources of heat.
Financial analysis and business case
Case Study: Northeast Georgia Medical Center, Braselton, GA
NGHS Braselton hospital in Georgia is an all-electric hospital that uses ground-source heat pumps to provide all heating and domestic hot water.
Greenfield New Hospital
As one of the “50 Best Hospitals” according to HealthGrades, NGHS wanted a project team that would create a total patient experience and use innovative ideas, evidence-based principles, and lean, value-oriented processes to create a sustainable healthcare destination. They selected Mazzetti as part of their integrated project delivery team and challenged us to re-think everything, including the design process itself.
Additionally, Mazzetti developed a ground-source heat pump system that uses the earth as a thermal battery and municipal grey water for additional heat rejection. Holes are bored 500 feet into the granite bedrock to store excess heat, which is then reclaimed when it is needed. This is a central-plant system that recycles internal energy to heat the building and make domestic hot water. No fossil fuels are burned on site – except for cooking and emergency power. Using the Lean A3 documentation method, the team demonstrated both lower capital cost and life cycle costs that are half that of a legacy central plant - $8M savings over 30 years.
The final design came in under budget – MEP construction cost came to $10/sf less than average for the Atlanta market, without compromise on patient experience or overall quality, and with unusually low projected operating costs.
Partners: HGA, Turner Construction
Size: 354,000 sf
Project Cost: $116M
Completion Date: 2015
Patient Tower & CEP Expansion
MEP engineering design services for the expansion of an existing patient tower previously designed by Mazzetti. The expansion will add 96 beds and a 9 bay nursery.
Emergency Department and Vertical Tower Expansion
Three floors on the existing patient tower: one interstitial utility floor, one floor of patient rooms, and one floor of shell space for future patient rooms.
- Expansion of Level 0 for new pharmacy, new laboratory, expansion of CSP, and MEP space.
- Expansion of Level 1 for ED.
- Shell expansion of Level 2 for future surgery.
- Mechanical space above Level 2 to serve the new ED.
- New elevator tower for the patient tower, from Level 0 to Level 11.
- Expansion of the Central Plant at Level 0.
Partners: Perkins&Will, Turner Construction
Size: 250,000sf
Project Cost: $300M
Case Study: Sutter Health
The 3rd floor of Sutter Health California Pacific Medical Center’s Stern Building was converted from a conventional CAV system with steam reheat to a VRF heat pump system. That system has been in operation for 14 years, working as designed with no issues, and providing the facility with the anticipated occupant comfort.
Comments
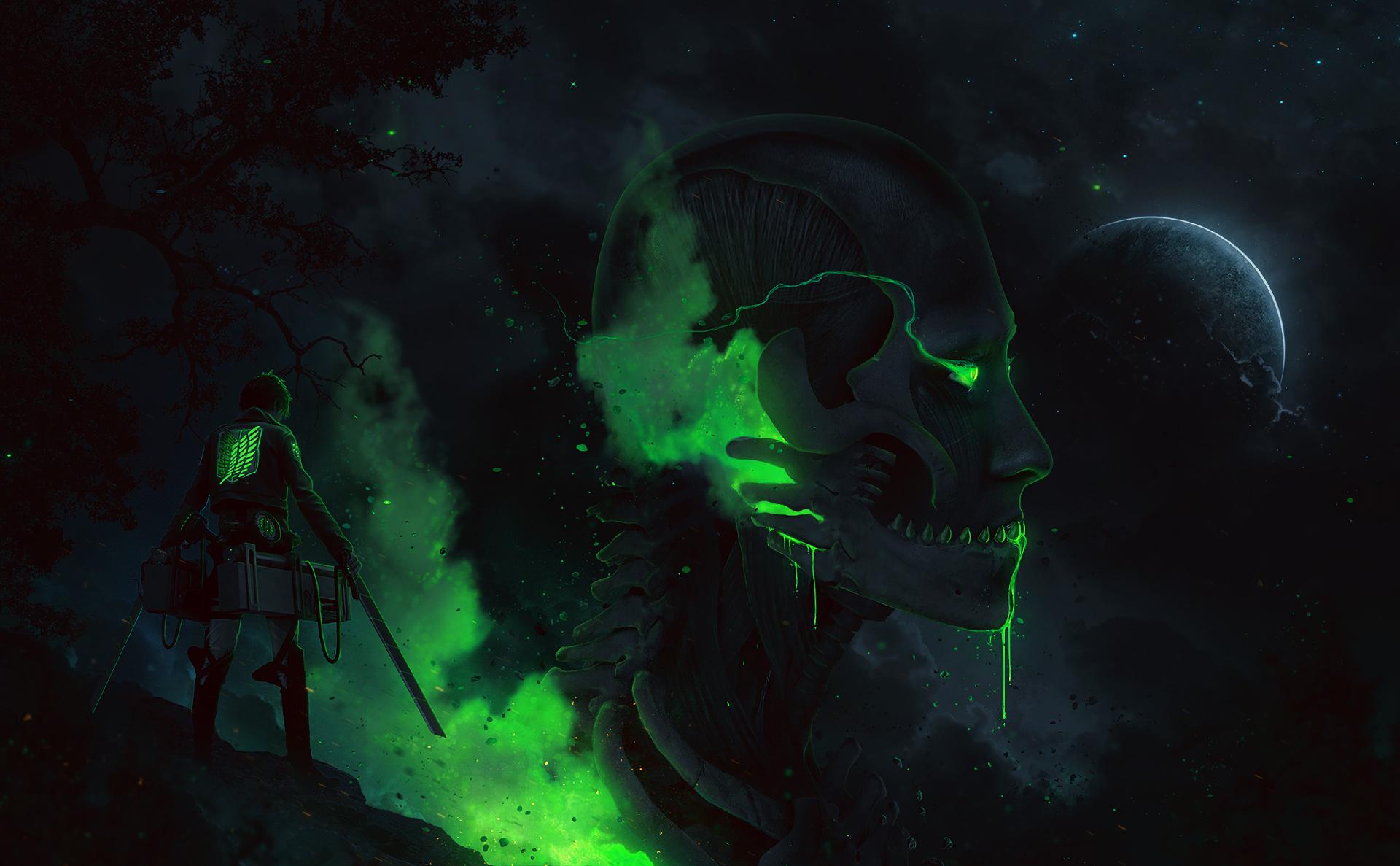
John Doe
8 seconds ago
Lorem ipsum dolor sit amet consectetur adipisicing elit. Quisquam, voluptatum. Lorem ipsum dolor sit amet consectetur adipisicing elit. Quisquam, voluptatum.
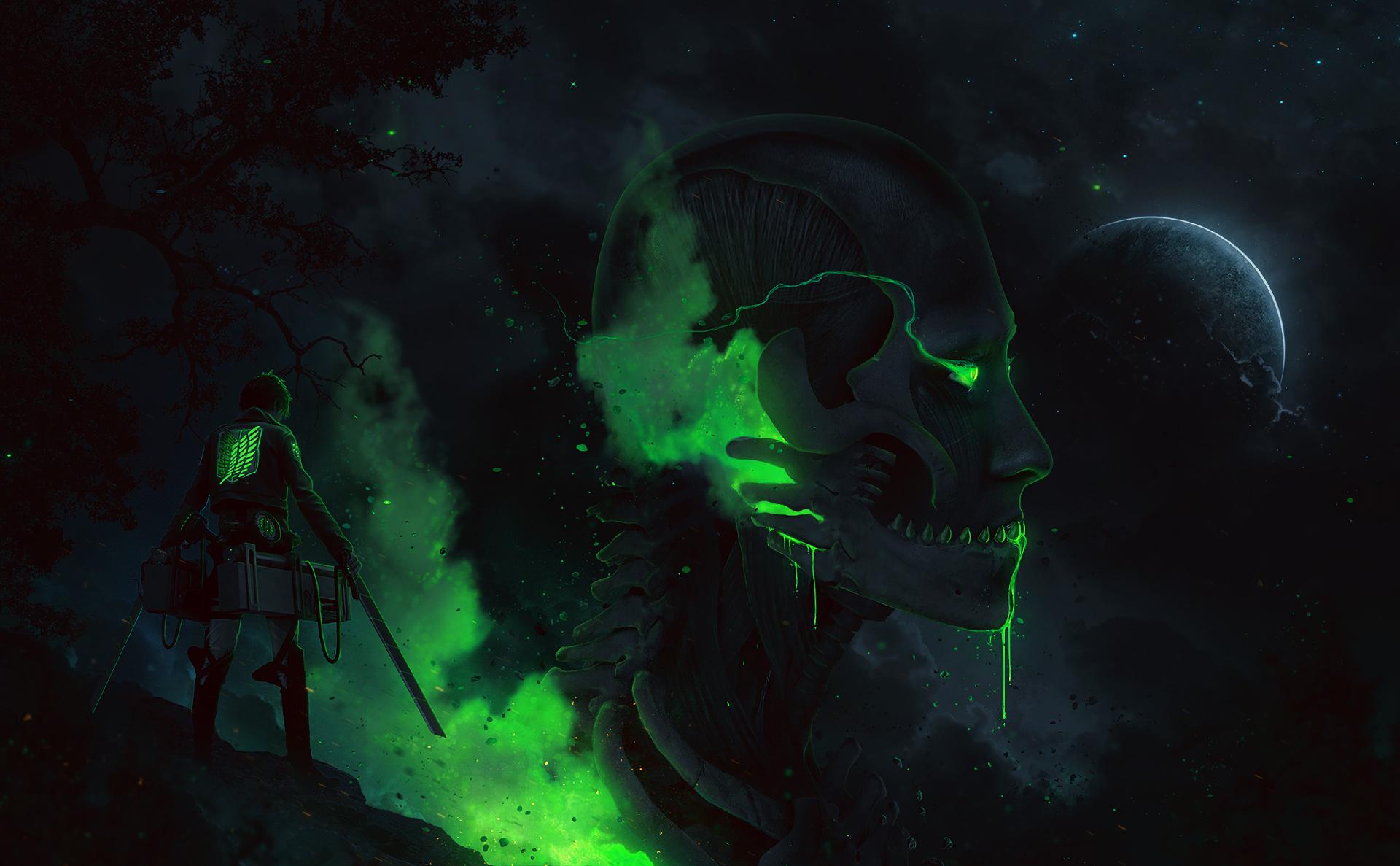
John Doe
18 seconds ago
Lorem ipsum dolor sit amet consectetur adipisicing elit. Quisquam, voluptatum. Lorem ipsum dolor sit amet consectetur adipisicing elit. Quisquam, voluptatum.