Welcome to the Decarb Guidebook
Approach
Benchmarking
Building Codes & Design Standards
State & Local Regulations
Technologies: Load Reduction
Technologies: Dehumidification
Technologies: If you must have a gas-fired boiler
Technologies: Central Plant
Technologies: Domestic Hot Water
Technologies: Steam
Technologies: Load Shifting and Energy Storage
Technologies: Emerging Technologies
Motivation Program
Pilot Projects
How to Pay for Decarbonization
Community Discussions
Workshops
Compressed Air Energy Storage (CAES)
Compressed air energy storage (CAES) is a method of storing energy that does not require the ...
Executive Summary
During periods of excess renewable energy capacity where production is greater than system loads, or at low time of use (TOU) energy pricing, an electric compressor is used to store atmospheric air at pressures up to 3000 psi, in existing caverns or storage tanks. When energy is required, the air is allowed to expand through a turbine or other pneumatic engine, generating electricity. This method was developed as an alternative to pumped hydrologic storage, which requires large amounts of concrete and has extensive environmental impacts. Two common types of compressed air energy storage (CAES) are adiabatic and diabatic.
Compressed Air Energy Storage (CAES)
Technical Description
Types of Systems
Adiabatic CAES (A-CAES) stores the heat of compression created during the charging process in a thermal energy storage system, and reuses it during the expansion, or discharging process which improves electricity production through the turbine [ease-storage].
Figure 1. A-CAES System Diagram
Diabatic CAES (D-CAES) does not store the heat of compression for reuse, and requires additional air cooling to increase air storage capacity. On discharge, the air must be heated to improve energy production through the turbine [ease-storage].
Figure 2. D-CAES System Diagram
Design considerations
CAES is primarily designed for use at the utility scale due to the large capacity available. Facility scale equipment is available, which would require storage tanks on site, instead of underground caverns.
From market research, the longest runtime seen was only 48 hours. For hospitals, NFPA-110 dictates that on-site emergency energy generation lasts 96 hours. Building owners should supplement with other on-site production.
Control strategies
Since it is a storage device, electricity can be produced at a moment's notice. The charging period, which is the length of time needed to fully pressurize the system, is determined by the ability of the compressor to pressurize the vessel. Storage capacity depends on the size of storage and the pressure it can withstand.
How does this decarbonize?
Air is used in a power generation device, instead of steam or natural gas. Combustion isn't required for power generation, so decarbonization is in the form of avoided combustion. The charging cycle can be done from renewable energy sources when available. However, should diabatic CAES be used, existing installations have shown that they use 67% less fuel than traditional combustion driven turbines, and much less emissions. Additional gas-scrubbing measures can be taken to curtail that further.
Implementation
Barriers: Technical
Most installations use underground caverns for storage which isn’t very economically sustainable as caverns can be difficult to find and could require extensive geologic excavation to utilize. Alternatively, pressure vessels can be used, but may be prohibitively expensive. The technology has been developed for utility scale power requirements (hence why most capacity nameplates are typically from 50-200 MW), not for a single facility.
Barriers: Culture
Although the technology isn’t new, it largely exists at the utility scale. Other renewable energies which also have storage abilities are more cost efficient. Additional pilot plants are needed in order to prove its viability, especially at smaller scales.
Strategy
CAES is site specific. Underground cavern structures can be excavated, but pre-existing formations are best. The earthen material should be of sufficient density and air-tightness, as determined by the desired level of pressurization If environmental conditions allow, such as an area which has pre-existing underground caverns or mines formed naturally or manmade, CAES could be a good candidate for supplying electricity for medical and university campuses, or off-grid military installations. Previously drilled holes for geologic exploration could also be utilized for air storage.
Financial analysis and business case
Additional funding from CEC is required to develop pilot plants. The technology is fairly well understood and systems are simple.
Case Study: Siemens McIntosh (Alabama) Power Plant
In 1991, Siemens Energy built the McIntosh plant in Alabama which has a capacity of 110 MW. Since then, it has had a 98% reliability rating. The plant is owned by PowerSouth Energy Cooperative, and is used for peak-load shifting, additional supply reserve, and frequency regulation for Southwest Alabama.
Case Study: Hydrostor San Luis 400 MW storage Facility
Hydrostor, a Canadian based company developing A-CAES, seeks to install a 400 MW/3,200 MWh storage facility in San Luis Obispo County. This facility requires a $820-million investment from the state of California, translating to 0.4 ¢/kWh, which is competitive with current PG&E rates.
Case Study: Hydrostor A-CAEs Toronto installation (2015)
The same company also completed a grid-connected A-CAEs installation in Toronto in 2015. The system was able to use off the shelf components and compressors. It uses hydrostatic pressure regulation, with the reservoir located 180-feet below Lake Ontario. The hydrostatic pressure maintains storage pressure, allowing for consistent output when needed.
Comments
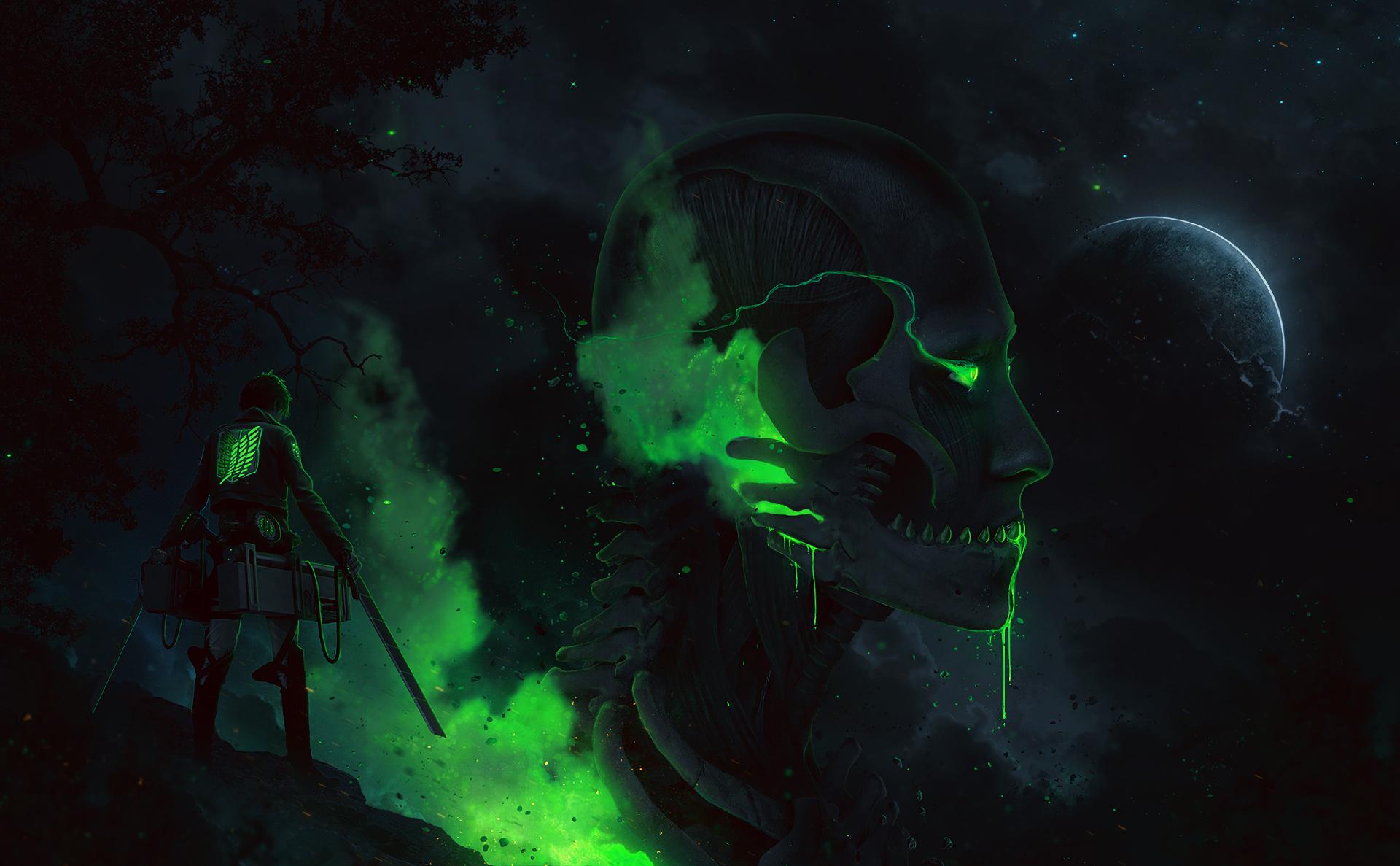
John Doe
8 seconds ago
Lorem ipsum dolor sit amet consectetur adipisicing elit. Quisquam, voluptatum. Lorem ipsum dolor sit amet consectetur adipisicing elit. Quisquam, voluptatum.
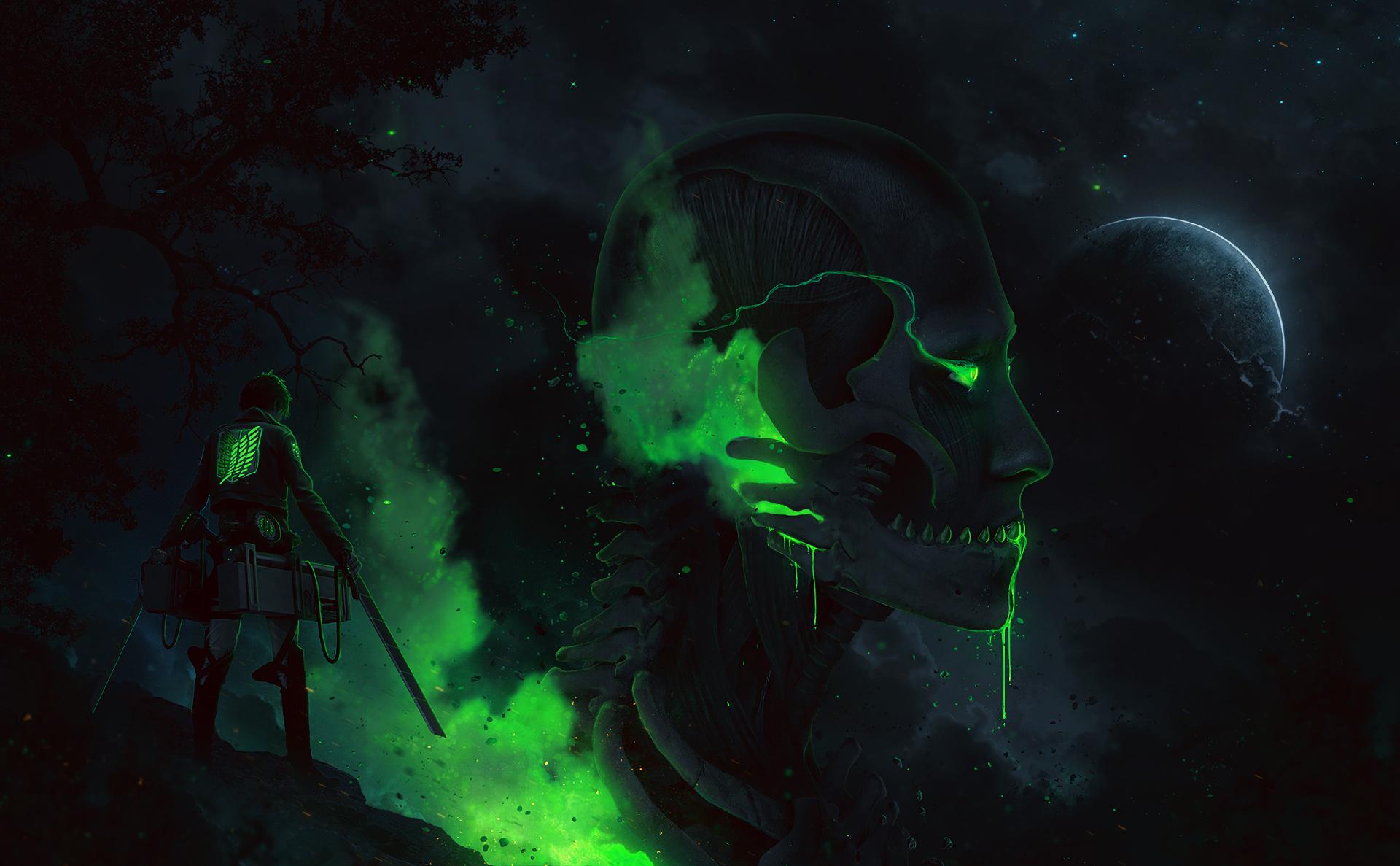
John Doe
18 seconds ago
Lorem ipsum dolor sit amet consectetur adipisicing elit. Quisquam, voluptatum. Lorem ipsum dolor sit amet consectetur adipisicing elit. Quisquam, voluptatum.