Welcome to the Decarb Guidebook
Approach
Benchmarking
Building Codes & Design Standards
State & Local Regulations
Technologies: Load Reduction
Technologies: Dehumidification
Technologies: If you must have a gas-fired boiler
Technologies: Central Plant
Technologies: Domestic Hot Water
Technologies: Steam
Technologies: Load Shifting and Energy Storage
Technologies: Emerging Technologies
Motivation Program
Pilot Projects
How to Pay for Decarbonization
Community Discussions
Workshops
Executive Summary
There have been studies that suggest a significant percentage of boilers currently installed are incorrectly sized for the application. A study in California investigated a number of buildings by trending the actual building loss compared to the installed boiler system equipment. In some cases, the installed equipment was 2 to 3 times higher than the average heating load. This would suggest the heating system is oversized for its application.
Most boiler installations are oversized rather than undersized. Oversized boilers often short cycle to satisfy low load conditions which makes it difficult to operate the boiler system efficiently and increases natural gas consumption, shortens the lifespan of the equipment, and increases emissions into the environment. Typically the reasons for oversizing are to provide additional capacity to ensure equipment is never undersized during unexpected increases in demand, or during equipment replacements where contractors will just match the capacity of the existing system without verifying current conditions with new load calculations. Various studies using trended load data suggest that oversizing boiler systems does not result in any realized benefits for building owners.
Specifying right-sized boilers requires verifying the proper boiler size using load calculations and actual load data to prevent repeating past mistakes. For decades, design engineers used an inefficient method to select boiler sizing by using the peak heating load to select capacity to be installed. However, this peak demand may only happen 1-2% of the year and result in the boiler cycling as it tries to meet the minimum or average load throughout the year. The peak heating load could be more than double the average load that the building experiences more than 98% of the year. Best practices for right sizing boilers include considering the building heating profile and tailoring equipment selection to efficiently operate at average heating loads rather than just the peak. This provides the benefits of decreased energy use, longer equipment life and a more efficient way to operate the heating system throughout the year.
Right-sized Boilers
Technical Description
Why the old way isn’t the best way?
For decades, design engineers have been specifying oversized boilers in commercial buildings. Boilers are sized based on peak heating loads, that is, to satisfy the coldest day of the year. However, the building only experiences peak heating load 1-2% of the year. This was the typical design methodology since it provided additional capacity to ensure equipment is never undersized, or oftentimes, when the boiler equipment is replaced, it would be replaced with the same size and new load calculations would not be conducted. Natural gas consumption and efficiency is not a priority in this design. Right-sizing the boilers is an interim step towards decarbonizing a building. Proper boiler size to ensure high efficiency operation at the most common or average building load, will lead to reduced natural gas consumption.
Design Considerations
In order to correctly determine the building heating load, load calculations should be derived from design indoor and outdoor air temperatures, exterior surface areas, and thermal construction properties. The information obtained from the calculation should closely reflect the expected heat loss. Designers should consider building occupant scheduling to account for building warm up and building operation profile. It is strongly recommended that the heating demand load and building operation schedule be reviewed throughout the year to determine maximum and part load conditions. This analysis is used to correctly size the boiler to efficiently control to part load operation, while also meeting maximum load. Boilers should be able to turndown efficiently and modulate boiler output to match building load.
Boiler turndown is the ratio of the boiler’s maximum heating output and the minimum heating output. The adjustment of the boiler heating output is achieved through modulating the burner. A well designed boiler turndown can match anticipated loads, which provides the following benefits:
More flexibility: The ability to match boiler operation with the actual building loads.
More efficient: If a boiler is producing more heat than the building needs to satisfy its demand, the remaining heat is exhausted. Boiler turndown allows the boiler to only produce the amount of heat necessary to match the current building load.
Avoiding boiler short cycling: When the building load is lower than the boiler’s output, the controller can rapidly switch the boiler on and off to try to meet the load, which is known as short cycling. Short cycling can cause equipment issues and reduce the useful life of the boiler.
Another way of considering boiler turndown is the use of multiple boilers. This method facilitates greater turndown ability and some redundancy.
If a single boiler fails, the remaining boilers can maintain operation, at a slightly lower heating output. The multiple boiler arrangement can be configured to better suit the actual heating loads. Condensing boilers also operate more efficiently at part load conditions.
The drawback to this approach is additional floor area is required to install multiple boilers while also allowing space for maintenance. Separate gas line connections to individual boilers, separate exhaust stacks, and drain piping are also required. In some cases this may not be feasible due to space constraints.
Another challenge is minimum flow capability. All traditional boilers have a stated minimum flow rate. This information is specified by the boiler manufacturer. This flow rate is dependent on the boiler heating capacity, minimum set output capacity, and firing rating.
Condensing boilers have no requirement for minimum water flow. For this reason a variable-speed primary only distribution is used to eliminate the need for by-pass flow around the boilers, which will minimize pump energy and boiler’s entering water temperature.
Best Practices
Understanding the building heat load:
Use this information to determine the appropriate boiler type to meet loads. For example, is the building load constant or does it vary?
Understanding the building heating profile to determine the proper boiler turndown to meet the load.
Control integration
Provide the ability to connect boiler controls to the central building automation system (BAS). This will allow the boiler performance to be evaluated in real time. Propose this capability be implemented in the boiler system performance specification.
Turn-down sizing
Discuss with the manufacturer to determine the optimum firing rate and turndown capability based on the selected boiler for the majority of the operating time.
Boiler efficiency
Recommend the use of condensing boilers to maximize boiler efficiency with the appropriate return water temperature. See Condensing Boiler section of the Guidebook for more information.
Propose stack economizer, or boiler blowdown to be used to capture wasted heat and direct it back into the system.
How does this decarbonize?
The decarbonization of healthcare facilities and commercial buildings will require the eventual phasing out of all fossil fuel based equipment. This includes natural gas fired boilers. However, phasing out gas-fired boilers is a challenge today and the economics are not always favorable towards electric powered equipment. That won’t always be the case, though. As an interim step in the path toward decarbonizing our healthcare facilities, reducing natural gas consumption through reducing loads and increasing equipment efficiency will provide a temporary improvement as future plans for full electrification are developed. That means taking steps to right-size the boilers and implement heat recovery where possible through smarter system designs. An improved design process to select the appropriately sized equipment for the building will help reduce a building owner’s capital equipment costs and operating costs by improving useful life of the equipment, reducing maintenance intervals, and improving energy efficiency.
Implementation
Barriers: Culture
Many engineers typically only use the calculated peak heat load and rules of thumb to determine boiler sizing, which results in oversizing. Engineers don’t like taking unnecessary risks and tend to overdesign to ensure the building will never have too little heat.
It takes additional effort (and cost) to build energy models to determine the peak building load and the heating profile throughout the year, to select boilers that will meet the building profile, and designing controls to maintain boiler operation during partial load conditions.
Barriers: Codes
The California mechanical code, Title 24, specifies under the HVAC systems requirements section, recommends safety factors be added to address unexpected loads, space changes along with steady state heating design of no more than 30%. The combination of heating and safety factors increases the possibility of 43% added capacity.
See below an excerpt from 2022 Multifamily and Nonresidential Compliance Manual:
Figure 1: Excerpt from Title 24 California Mechanical Code, 2022 Multifamily and Non-residential Compliance Manual
The statement suggests two methods be used to determine heating load warm up. Item “12.b” proposes applying no more than 30% safety factor to steady state heat load calculations. Recommend that the application of the safety factor be carefully reviewed and not simply added to calculations without consideration. Adding the proposed safety factors will lead to oversized heating system equipment and does not aid in matching the building load profile.
Strategy
Strongly recommend the approach of conducting building energy analysis modeling to support equipment selection. Perform commissioning on boiler operation and boiler turndown to ensure the equipment controls are tied into the BAS properly and ensure the operation and performance of the heating hot water system. Include devices that will monitor gas input, boiler output, and Btu meters on the distribution side.
Financial analysis and business case
Oversizing the heating hot water system can have significant cost implications. Larger boilers have higher first costs, higher maintenance costs, and higher operating energy costs. If that boiler is only used at less than 30% of its rated capacity for 99% of the year and only to 75-80% of its rated capacity the other 1%, then most of that increase in cost is wasted. At the time of this research, a true life cycle cost analysis of a properly sized boiler system was not available but there is a need for one. Please reach out to the Decarb:Healthcare team if additional LCCA or financial business case info is available.
Case Study: Kaiser Milpitas MOB
Kaiser Milpitas MOB, Milpitas, CA:
The existing hot and cold dual duct HVAC system will be replaced with a variable refrigerant system (VRF). The heating load will be addressed in the VRF system. We will consider the preliminary building load calculations and use it to illustrate boiler right sizing.
The two-story building is approximately 45,500 square feet The heating load calculations were based on design outdoor and indoor temperatures and the building construction’s thermal properties. An energy model was used to estimate the building’s heating profile throughout the year. The peak heating load is 460,000 btu/hr (10.1 btu/sf) and the average heating load, or the building heating profile, is 66,000 btu/hr (1.4 btu/sf). The graph below shows the annual heating load profile.
The peak heating load condition occurs 1.5% of the 8760 hours/year. The average heating load is roughly 14% of the building peak. This is where boiler oversizing becomes an issue. Some diversity must be applied to the overall building load to account for much of the heating load. The above building profile indicates the proposed equipment selection.
In this case, the recommendation is to install a boiler with a minimum turndown ratio of 10:1. Discussions with the boiler manufacturer confirmed the optimum firing rate will be achieved at the lowest turndown setting. For the <1% of hours where the building heating load exceeds the boiler output capacity, supplemental heating will be used in the form of unit heaters or electric resistance reheat.
Comments
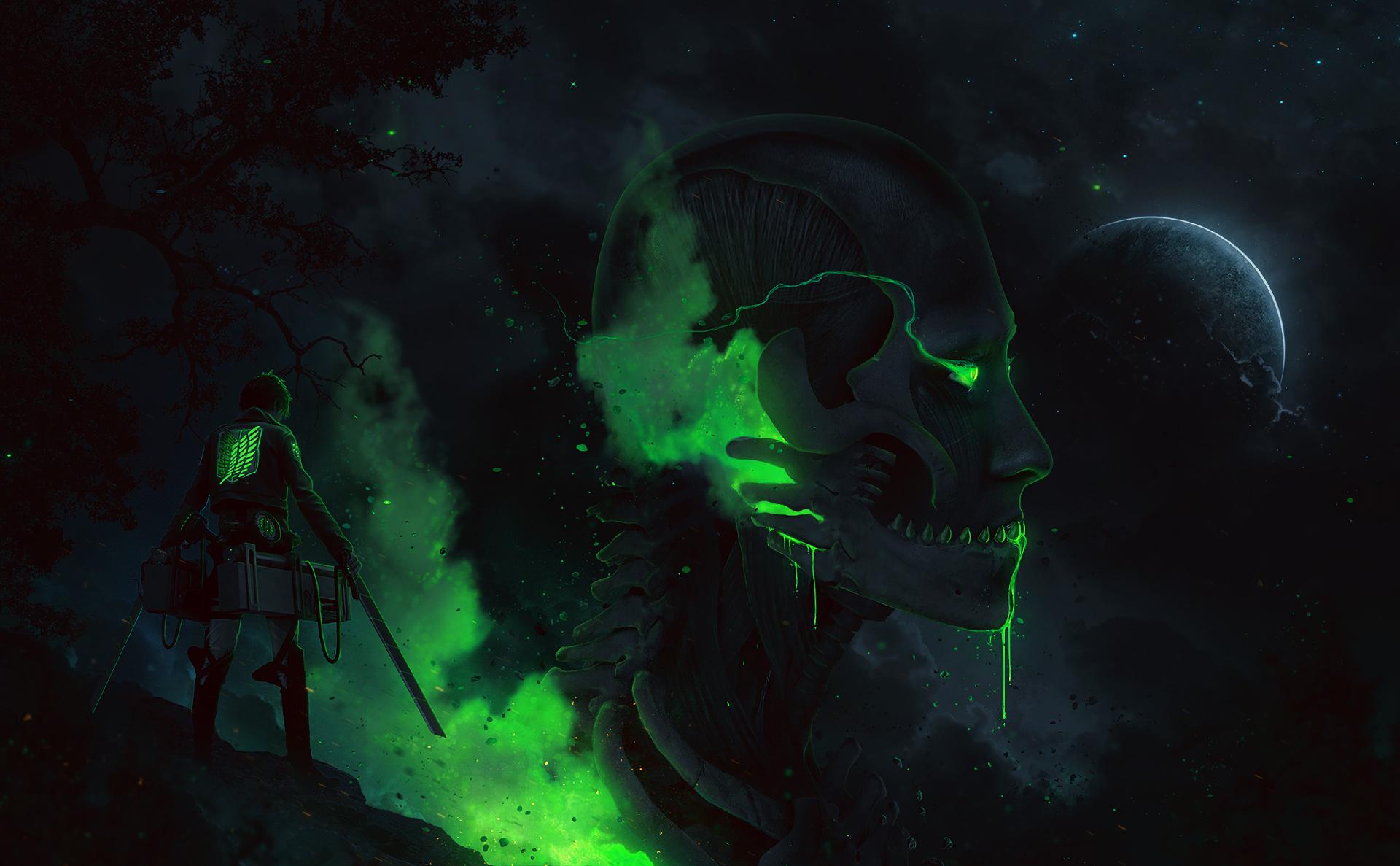
John Doe
8 seconds ago
Lorem ipsum dolor sit amet consectetur adipisicing elit. Quisquam, voluptatum. Lorem ipsum dolor sit amet consectetur adipisicing elit. Quisquam, voluptatum.
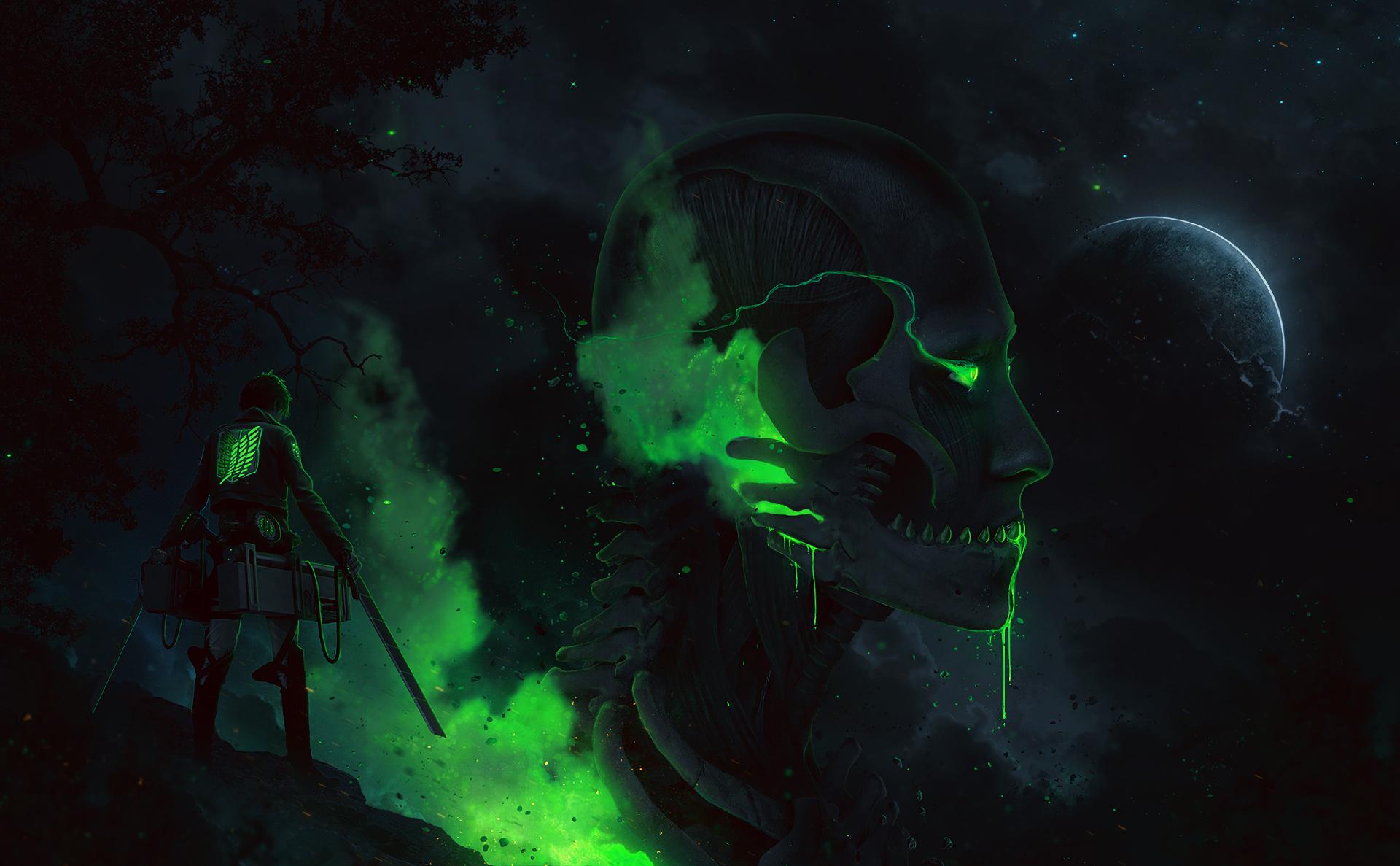
John Doe
18 seconds ago
Lorem ipsum dolor sit amet consectetur adipisicing elit. Quisquam, voluptatum. Lorem ipsum dolor sit amet consectetur adipisicing elit. Quisquam, voluptatum.