Welcome to the Decarb Guidebook
Approach
Benchmarking
Building Codes & Design Standards
State & Local Regulations
Technologies: Load Reduction
Technologies: Dehumidification
Technologies: If you must have a gas-fired boiler
Technologies: Central Plant
Technologies: Domestic Hot Water
Technologies: Steam
Technologies: Load Shifting and Energy Storage
Technologies: Emerging Technologies
Motivation Program
Pilot Projects
How to Pay for Decarbonization
Community Discussions
Workshops
Converting from Steam to Hydronic heating
Facilities with steam boiler plants and steam piping serving all heating and steam needs are ...
Converting from Steam to Hydronic Heating
Technical Description
Background
Many steam systems with a central plant use heat exchangers located at site of use to heat domestic and heating hot water. Consider a steam system that provides domestic hot water (DHW) and heating hot water (HHW) in addition to providing steam for sterilization and humidification. At the heat exchange for distributed steam and HHW, the hot water temperature may be 160℉. Whereas the HHW supplied by a heat recovery chiller may be 120℉. Due to lower operating temperature of hot water systems, more surface area and effective areas for heat transfer are needed. Thus, radiators would need to be reconsidered and heat exchangers would need to be replaced with appropriately sized water-to-water units.
Older steam infrastructure is built on a single pipe configuration wherein the hot steam rises toward the radiators and condensed water falls toward the return. In this case, there is not any HHW infrastructure that can be reused.
Figure 1. Single pipe configuration steam heating
Efficiency and the coefficient of performance are both used to describe the ability of a system to produce heating or cooling. Coefficient of performance (COP) is a measure of how much useful energy an energy conversion system produces per unit of energy consumed. It is specifically used for systems that produce heating or cooling. For example, a heat pump with a COP of 4 produces 4 units of heat for every unit of energy it consumes. In the case of a natural gas boiler, the COP is the equipment efficiency expressed as a decimal: 0.79.
A well designed hydronic heating system is the backbone for any thermally based renewable energy system and provides opportunity for renewable thermal technologies that often cannot supply heat to a system operating above 140 degrees Fahrenheit.
Decoupling the source of heat for space heating from the source that supplies steam for sterilization and humidification provides the opportunity to plan for alternative steam generation techniques. Meeting steam load requirements for hospital functions outside of space heating:
- Electric steam production for sterilization and dishwashing
- Adiabatic system for humidification
Replacing Central Plant Equipment
HHW and DHW uses
Producing hot water instead of steam via heat pumps can be done with a COP ~ 3. With a heat pump chiller, hot water can be partially to fully provided for by the heat extracted from the chilled water. A central plant approach to heat pumps will provide great efficiencies in equipment and maintenance. For large facilities and campuses, extensive hot water piping would be needed.
Chilled water uses
Steam-absorption chillers running on natural gas have COP ~ 1.5, but are relatively cheap to operate given the comparatively low price of gas. Centrifugal chillers running on electricity have a COP ~ 5.5.
Replacing (location-of-use) infrastructure
Heating hot water coils
Zone level data can help determine if existing coils are adequate at lower HHW temperatures (falling from the neighborhood of 160℉ to 120℉). When replacement is necessary, the coils will be larger so both AHUs and terminal units should be verified for allowable space as part of retrofit planning. Re-calculating the coil capacities to right-size the equipment is also recommended as a potential cost-saving exercise.
Steam to hot water heat exchangers
For a steam system that provides HHW, the HHW pipes after the exchangers could be reused but the heat exchangers themselves must be replaced with water-to-water units.
Design considerations
In considering options for how to electrify, decarbonize, and convert from steam to hydronic heating, capital and operating cost will have a large impact. The technologies proposed within this section- heat pumps, heat recovery chillers, and electric boilers - are expensive compared to a natural gas boiler and they operate on the more expensive utility. The capacity of the current electrical system supplying to the building as well as the remaining lifespan of the steam boilers provide energy for peak load and resilience within the new master plan?
Can infrastructure for both exist at once?
What is the facility's potential for solar thermal technology within the near future?
Advantages
Hydronic systems are better suited to be paired with renewable energy sources, heat pumps and thermal storage.
- Solar thermal heating integration
- Geothermal energy source integration
- Thermal storage integration
Uneven heating within steam systems is a common issue that is significantly easier to balance within a hydronic system. Steam systems typically require a full time boiler operator, on shift 24/7. Therefore, a conversion to a hydronic system provides a operational cost saving
How does this decarbonize?
Generally, hydronic systems operate with lower thermal losses. On principle of higher efficiency they use less natural gas. However, note that this comparison exists in the non-optimal situation where natural gas is still used. The real potential for converting from steam heating to hydronic heating is the utilization of renewable thermal heating and high performing heat pumps to offset natural gas use.
Implementation
Barrier: Codes
Converting from steam to electrified Hydronic heating will increase the facilities reliance on the electric grid. An NFPA 110 level 2 emergency power supply system may be required to resize (an additional generator) to accommodate the new electrical load in case of a grid outage.
Barrier: Culture
Building operators are long familiar with the operation and maintenance of a steam plant. New technology will pose challenges with maintenance and finding service technicians.
The financial business case for this type of project is hard to make. Consider for a moment a project: the hydronic piping infrastructure alone will cost $3.5M and the internal rate of return for the entire project is 5.6%. For a retrofit project, the business case heavily lies within decarbonization.
Barrier: Technology
Converting a facility to hydronic heating is a large endeavor that will require renovation in and outside of the central plant. In many cases, regardless of the electrification approach, a new hot water distribution loop is needed. Existing condensate piping will be dramatically undersized for use in a hydronic system. Circulator pumps are required in a hydronic system.
There is not enough heat outdoors within the coldest weather for heat pumps to operate independently. The steam infrastructure can therefore be kept to provide this supplemental heat and to serve as a backup during either power failure or machine maintenance.
Strategy
Adjust Master Plan efforts to codify not adding any new steam-using systems. Benchmark the facilities operation by determining the peak demand, the energy load required for space heating, the energy load required for hot water supply - whatever the current steam end-using system is. Install sub-metering and conduct a study to quantify these items and size new technology. The boiler is often oversized; designing the new system by relying on existing equipment capacity will potentially lead to unnecessarily high capital costs. The boiler is often oversized; oversized systems will negatively impact performance
Inconsistencies between expected and measured performance may reveal areas for improvement - replacing 3 way valves, eliminating other bypass means, and temperature resets - ensuring a reduction in energy consumption and a well-informed foundation for retrofit planning.
If a facility is already due for a major renovation, the conversion from steam to hydronic heating may be an attractive opportunity since transitioning the space heating system will likely involve opening walls and floors to replace piping and associated fixtures when the steam to hot water heat exchangers exist outside of the central plant. Piping can be sized specifically for hot water, eliminating the need to use valves on oversized lines that were originally calculated for steam. Balancing the supply and return of water is much simpler if piping is adequately sized. Radiators can be replaced with more efficient alternatives, such as hydronic floor heating systems or water-source heat pumps. Automation can be deployed for the entire hot water system, achieving the lowest possible operating cost.
Financial analysis and business case
The reality of any project that moves an existing campus or facility away from steam is that there will be major initial costs.
Table 1. The estimated cost for electrical equipment includes the differential cost between a 350 kW generator vs. a 400 kW generator. This is to provide enough Code-required heating on emergency power for the ASC.
Case Study: University Building Cluster, San Diego
A cluster of three university buildings, located in San Diego, transitioned from a cogeneration plant with steam-to-hot water converters at each building to local heating hot water plants. [1] The client in this case aspired to achieve carbon neutral status within the next 15 years. The main driver of this project was the failing steam infrastructure. A Hybrid option was implemented to maintain resilience while reducing carbon emissions to a third of the anticipated emissions from a baseline option of gas-fired condensing boilers. The plant would operate using a water-cooled heat recovery chiller (with the heating hot water supply temperatures set to 110℉) to provide 80% of the building’s heating hot water (HHW) needs (roughly 25% of peak capacity). The HRC operates only in heating mode with a COP of 7.0. Supplemental gas-fired boilers provide additional heating during peak capacity or during ambient temperatures below 40℉; during which the system HHW supply is 135℉.
Comments
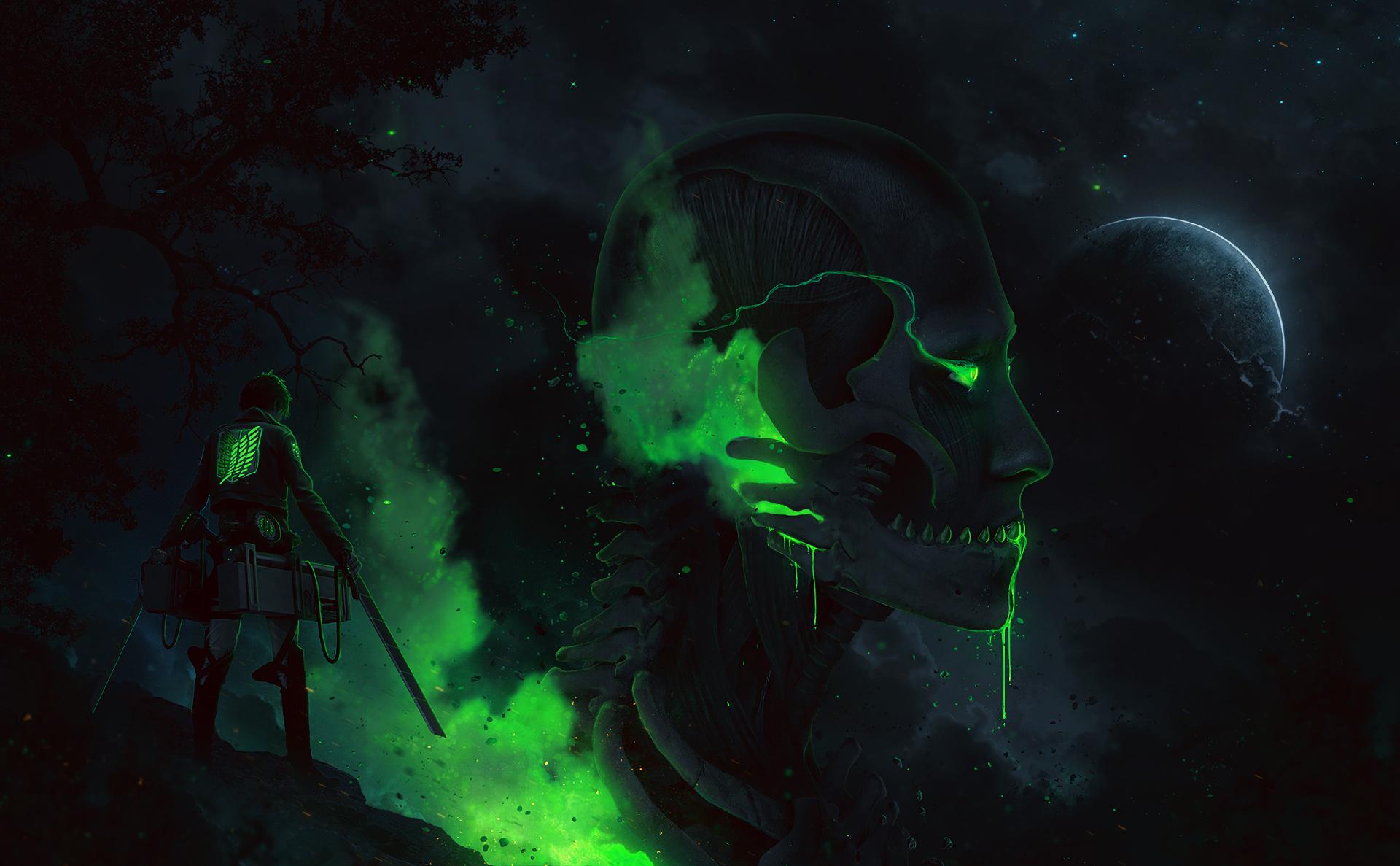
John Doe
8 seconds ago
Lorem ipsum dolor sit amet consectetur adipisicing elit. Quisquam, voluptatum. Lorem ipsum dolor sit amet consectetur adipisicing elit. Quisquam, voluptatum.
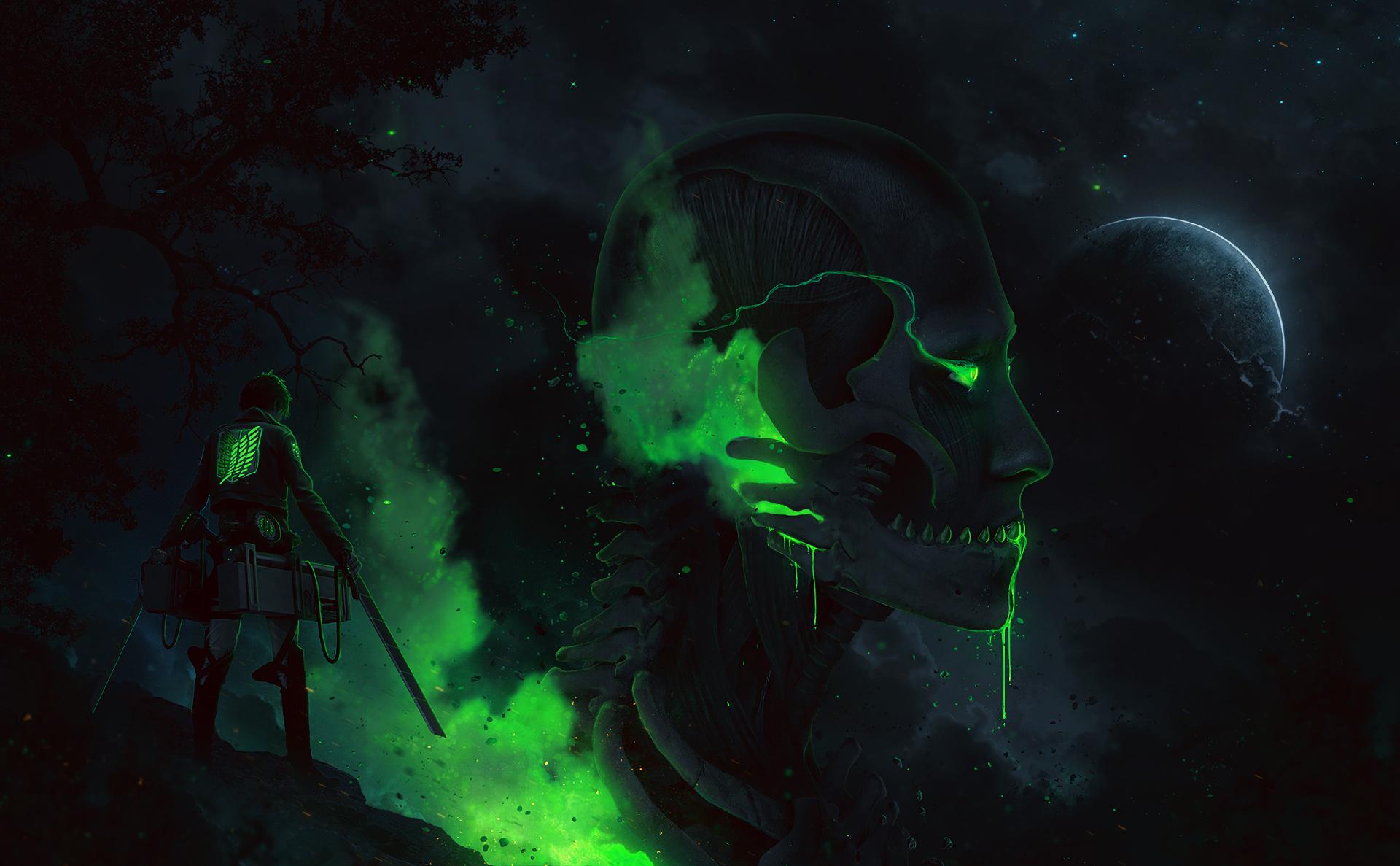
John Doe
18 seconds ago
Lorem ipsum dolor sit amet consectetur adipisicing elit. Quisquam, voluptatum. Lorem ipsum dolor sit amet consectetur adipisicing elit. Quisquam, voluptatum.